Microfluidic Droplet Production Method
Micro-droplet production is one of the most widely used microfluidic activities. It consists of the encounter of two immiscible liquids flowing perpendicularly in microchannels, resulting in the formation of micro-sized, highly-monodisperse droplets.
Most commonly, droplets of water in oil are made. In this section, we describe the principle behind droplet formation in microfluidic channels, as well as the various production regimes and their advantages and drawbacks.
Definition of droplet microfluidics
Droplet microfluidics is a powerful tool which consists of generating and manipulating micron sized monodispersed droplets. Microfluidic based droplet control and generation allows for:
- Highly monodispersed droplet production, unlike other batch emulsion methods using “in-line” continuous droplet production
- Single droplet manipulation as an individual pL scale biochemical reactor
- Miniaturization of production and bioanalytical devices via droplet generation
Microfluidics-based droplets have many diverse and varied applications, including particle synthesis [1] and physicochemical analysis [2].
Good control of droplet production can also make single-cell analysis [3] or drug testing possible [4][5].
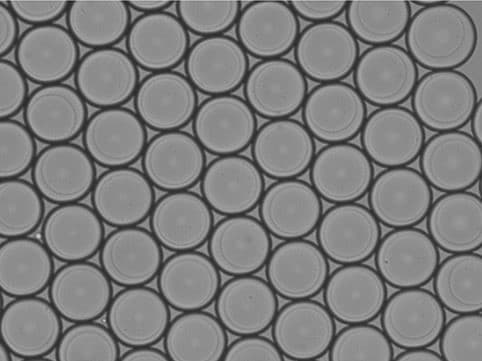
How are droplets generated in microfluidics?
The droplet generation method in microfluidics is based on the use of two immiscible fluids, usually oil and an aqueous solution. The droplets are made in devices called microfluidic chips. Different physical aspects are involved in the droplet production method, depending on the design and materials of the microfluidic chip. Among all chip designs to generate droplets, three are widely used in the field of microfluidics.
A co-flow, a T-junction and Flow Focusing design [6][7][8][9].
Droplet production in a co-flow design
The co-flow design for droplet production consists of two concentric capillaries with the inner capillary carrying the dispersed phase and the outer capillary carrying the continuous phase. As the dispersed phase enters the main channel, the viscous stresses created by the continuous phase stretch the interface until it breaks forming a droplet [7][10] [11][12] [13]
One of the main advantages is the simple design of the co-flow.
Nevertheless, the droplet size and frequency remain limited in this kind of design.
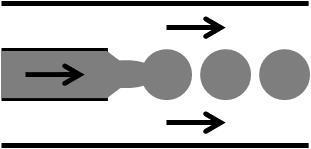
Droplet production in a T-junction design
First highlighted by Thorsen et al in 2001 [16], this technique is the simplest and most commonly used to generate droplets in a controlled way. In a T- junction, the dispersed/internal phase is injected perpendicularly to the flow of the continuous/external phase to generate microfluidic droplets.
When the immiscible fluids arrive at the T-junction of the two channels, the dispersed phase progressively enters the main channel. The continuous phase shears at this point. The dispersed phase then forms a bend at the interface of the two fluids. The more the dispersed phase advances in the main channel, the more the elbow narrows to a break in the continuity of the interface. The break generates the detachment of a drop that continues to move in the direction of the flow of the channel. [17][18][19]
The advantages of this method of droplet production are the simplicity of the design and the great knowledge of the physical phenomena involved in droplet “break-up”, which allows for better understanding and control of the droplet generation process. In the T-junction design, it is very easy to control the droplet frequency and size. However, the frequency and size ranges remain limited by the chip design and materials.
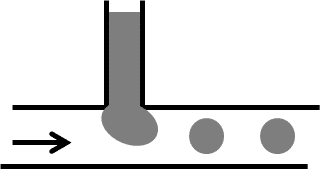
Droplet production in a flow-focusing design
As demonstrated by Anna et. al. in 2003 [14]
In a flow-focusing design, the dispersed phase is introduced directly into the main channel, while the continuous phase is injected by two branches placed perpendicularly. The dispersed phase is then pinched on both sides by the continuous phase, and a droplet is formed due to the competition between the viscous force and the surface tension at the interface between the two phases [15]. One of the big differences with the T-junction design is the symmetry of the flow-focusing design.
The advantage is that the symmetric design and physics effect allows one to have more flexibility in terms of droplet size and droplet frequency. The symmetric design allows for droplet generation which is more sensitive to the flow of the two phases. The knowledge and control of droplet “break up” phenomena remain limited.
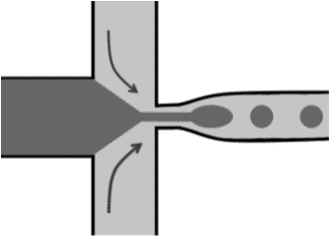
Which production regime fits my needs?
In a microfluidic droplet production method, several regimes of droplet formation are observable, depending on the experimental conditions:
The “squeezing” regime leads to a plug-shaped drop flow that occupies the entire width of the channel with a length-to-width ratio greater than 1. The size of plugs obtained depends mainly on the flow rates of the dispersed and continuous phases. The rupture of these plugs is due to the pressure drop in the main channel resulting from the presence of the dispersed phase.
The “dripping” regime leads to a flow of drops of spherical shape and dimension close to the width of the channel. In this case, the viscous shear forces cause the detachment of the drops.
The jetting regime is characterized by the generation of drops far from the intersection of the two phases. The drops generated are much smaller than the width of the channel and are generated at a very high frequency.
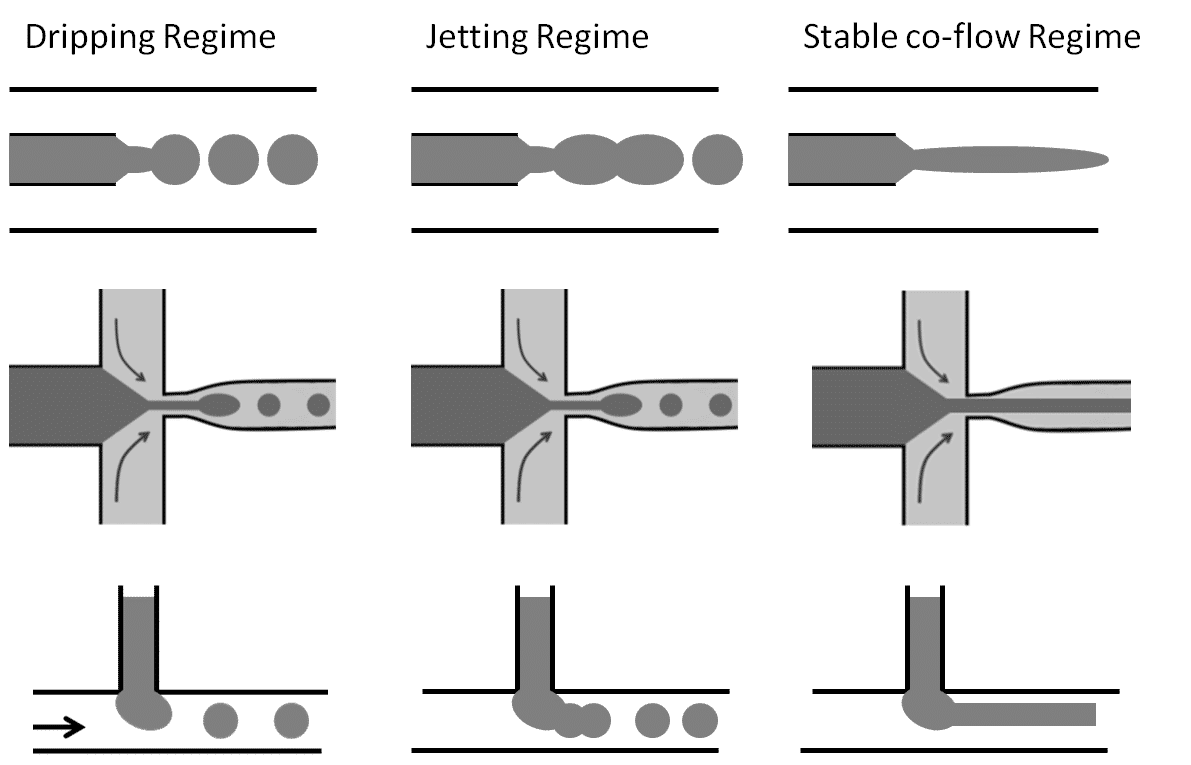
Overview of Drop Seq application in microfluidics
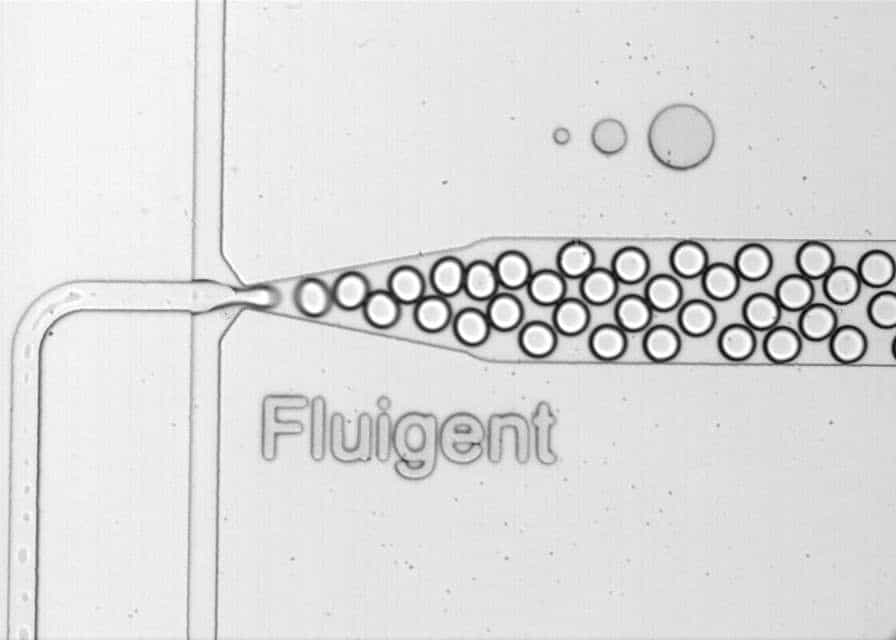
DNA and its expression are at the heart of cellular mechanisms, but our knowledge of cells and their diversity remains limited and incomplete. Study is essential to understand the development, functioning and reproduction of living beings, especially since mutations are at the origin of numerous pathologies (cancer, autoimmune disease, diabetes …). The currently available methods to determine and sequence the genome do not allow us to fully understand the functioning of DNA.
Drop seq and In drop are methods / technologies that use microfluidics to tackle this issue by providing the ability to target thousands of individual cells simultaneously by encapsulating them in tiny droplets for parallel analysis.
Recent advances in dPCR for microfluidic application
PCR (Polymerase chain reaction) is a well-known and widespread technique in molecular biology. It allows for amplification (with a multiplication factor of the order of one billion) of a known DNA or RNA sequence.
Currently, microfluidics has enabled a new technique which consists of single cell and PCR mixture encapsulation into microdroplets. The high droplet generation frequency and the low volume of the microfluidic system allow one to increase the number of amplifications possible while reducing the cost of reagent consumption.
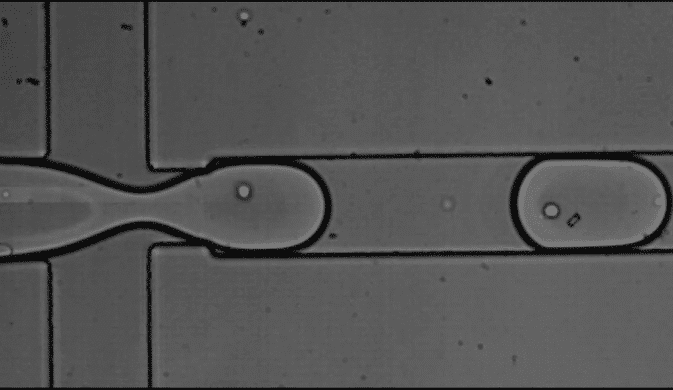
The Fluigent Droplet Production Starter Pack
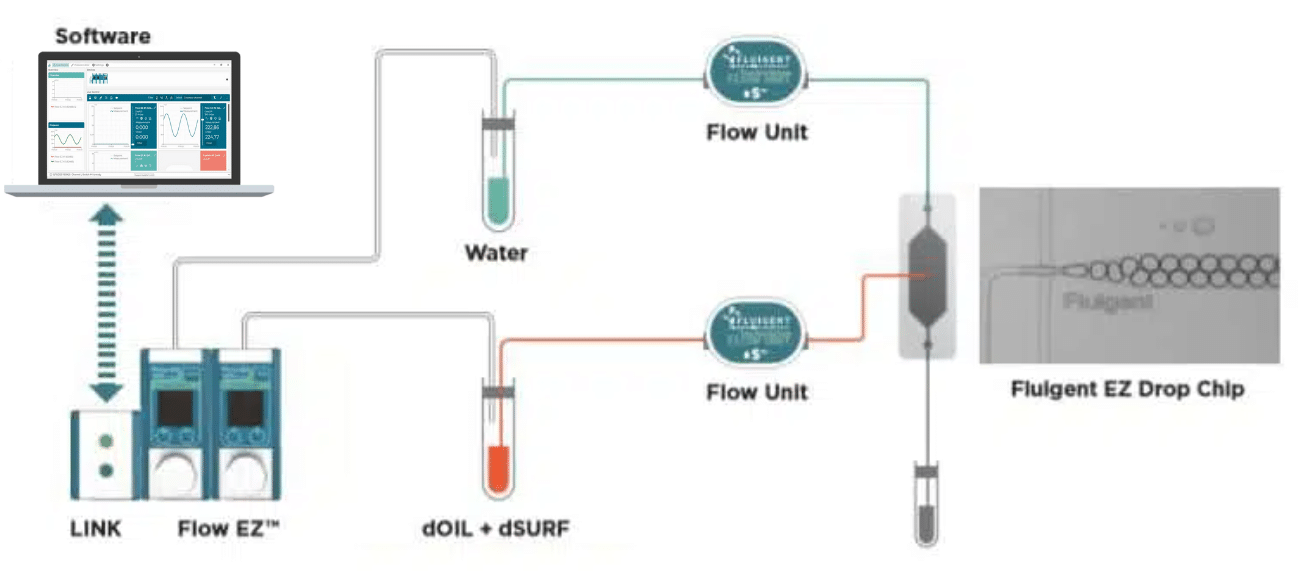
The Fluigent Droplet generation pack provides an easy droplet production method with total control of droplet size and frequency. The droplet generation pack provides all items needed to generate droplets, including pressure controllers, the chip and the surfactant.
In this pack, Fluigent gives you:
- Pressure controllers: Flow EZ
- Flow sensors: Flow Unit
- Droplet generation chip: EZ-Drop
- Continuous phase with surfactant: dSURF
- Tubing pack with reservoir
Complex emulsion production platform
The Complex emulsion production platform is a platform dedicated for droplet production and complexe emulsion such as double emulsion, microcapsules…
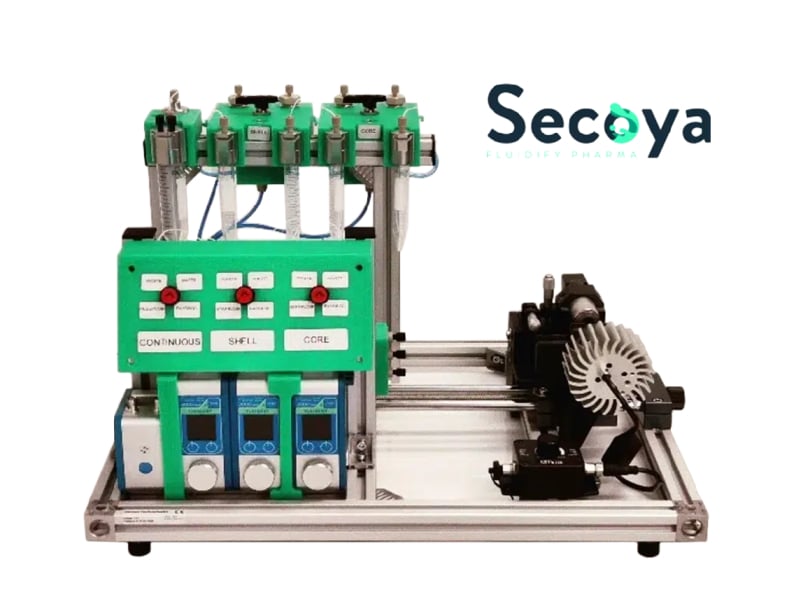
This easy to use platform allow to use and control the production of droplet to to target multiple applications :
Related Resources
- Microfluidic Application Notes
Water in Oil Emulsions
Read more - Microfluidic Application Notes
Oil in Water Emulsions
Read more - Microfluidic Application Notes
Generating a water emulsion in an oil solution using a droplet generator chip
Read more - Microfluidic Application Notes
Double Emulsion Generation
Read more - Microfluidic Application Notes
E. Coli Culture in Droplets Using dSURF Fluorosurfactant
Read more - Microfluidic Application Notes
Encapsulation of Cells In Small Double Emulsions
Read more - Microfluidic Application Notes
Droplet Sequencing: Drop-Seq method
Read more - Microfluidic Application Notes
Encapsulation of multiple emulsions in a single droplet
Read more - Microfluidic Application Notes
Alginate Microbeads Production
Read more
References
[1] Jean-Christophe Galas, Denis Bartolo and Vincent Studer, « Active connectors for microfluidic drops on demand », New Journal of Physics, n°11, 075027, 2009
[2] M. C. Jullien, et al., “Droplet breakup in microfluidic Tjunctions at small capillary numbers”, Physics of fluids, n°21, 072001, 2009
[3] Macosko et al, “Highly Parallel Genome-Wide Expression Profiling of Individual Cells Using Nanoliter Droplets, n° ,pp 1202-1214, 2015
[4] L. Yu, M. C. W. Chen, K. C. Cheung, “Droplet-based microfluidic system for multicellular tumor spheroid formation and anticancer drug testing”, Lab Chip, n°10, pp. 2424-2432, 2010
[5] Shembekar et al, « Droplet-based microfluidics in drug discovery » Lab Chip, n°16, pp. 1314-1331, 2016
[6] Ralf Seemann et al, « Droplet based micro?uidics », 2011
[7] Tomasz Glawdela, Caglar Elbuken and Carolyn L. Ren, « Droplet Generation in Microfluidics », 2013
[8] Pingan Zhuab and Liqiu Wang, « Passive and active droplet generation with microfluidics: a review » , Lab Chip, n°17, pp. 34-75, 2017
[9] G F Christopher and S L Anna, « Microfluidic methods for generating continuous droplet streams », 2007
[10] Pingan Zhu · Xin Tang · Liqiu Wang « Droplet generation in co?flow microfluidic channels with vibration », 2016
[11] C. Cramer, P. Fischer, and E. J. Windhab, 2004. “Drop formation in a co–flowing ambient fluid,” Chemical Engineering Science, vol. 59, pp. 3045–3058
[12] Y. Hong and F. Wang, 2007. “Flow rate effect on droplet control in a co-flowing microfluidic device,” Microfluidics and Nanofluidics, vol. 3, pp. 341–346
[13] R. Xiong, M. Bai, and J. Chung, 2007. “Formation of bubbles in a simple co–flowing microchannel,” Journal of Micromechanics and Microengineering, vol. 17, pp. 1002–1011,
[14] Shelley L. Anna, Nathalie Bontoux and Howard A. Stone, « Formation of dispersions using ‘‘?ow focusing’’ in microchannels », 2002
[15] A. M. Ganan-Calvo and J. M. Gordillo “Perfectly monodisperse microbubbling by capillary flow focusing,” Physical Review Letters, vol. 87, p. 274501, , 2001
[16] T. Thorsen, Richard W. Roberts, Frances H. Arnold et S.R. Quake : Dynamic pattern formation in a vesicle-generating microfluidic device. Physical Review Letters, 86(18):4163–4166, 2001
[17] Tomasz Glawdel • Carolyn L. Ren , « Global network design for robust operation of micro?uidic droplet generators with pressure-driven ?ow », 2012
[18] Evandro Piccin, Davide Ferraro, Paolo Sartori , Enrico Chiarello, Matteo Pierno, Giampaolo Mistura, « Generation of water-in-oil and oil-in-water microdroplets in polyester-toner microfluidic devices », 2014
[19] Qiang Liao, Shu-Zhe Li, Rong Chen, Hong Wang, Xun Zhu, Wei Zhang, and Xue-Feng He, « Coalescence with droplets caused acceleration of the liquid movement in microchannels »,2015
Related products
-
Encapsulation Platform for FACS Read
-
Microfluidic Droplet Pack Read
-
Drop-Seq Pack Read
-
Easy droplet generation chip Read
-
PDMS Drop-seq chip for Drop-seq experiments Read
-
Microfluidic Double Emulsion Device Read
-
Microfluidic Complex Emulsion Production Platform Read
-
Double Emulsion Generation Pack Read
-
Highly stable fluorosurfactant for microdroplet generation Read
-
Microfluidic Single Emulsion Device Read