OEM Case Study: Microfluidic Drug Screening
With this case study, we present an OEM challenge faced by a client, and how Fluigent addressed it by supporting the development and providing knowledge for the fabrication of an instrument for automated microfluidic drug screening.
“Fluigent’s expertise enabled us to completely change the scale of our microfluidic protocols, from the Ph.D. student experiment to the fully automated and parallelized workflow available for anyone. In addition to accompanying us in this process with their ideas and multi-disciplinary skills, Fluigent’s support and responsiveness are first class!“
Anonymous Customer
The challenge of turning a lab bench microfluidic system into a commercial device
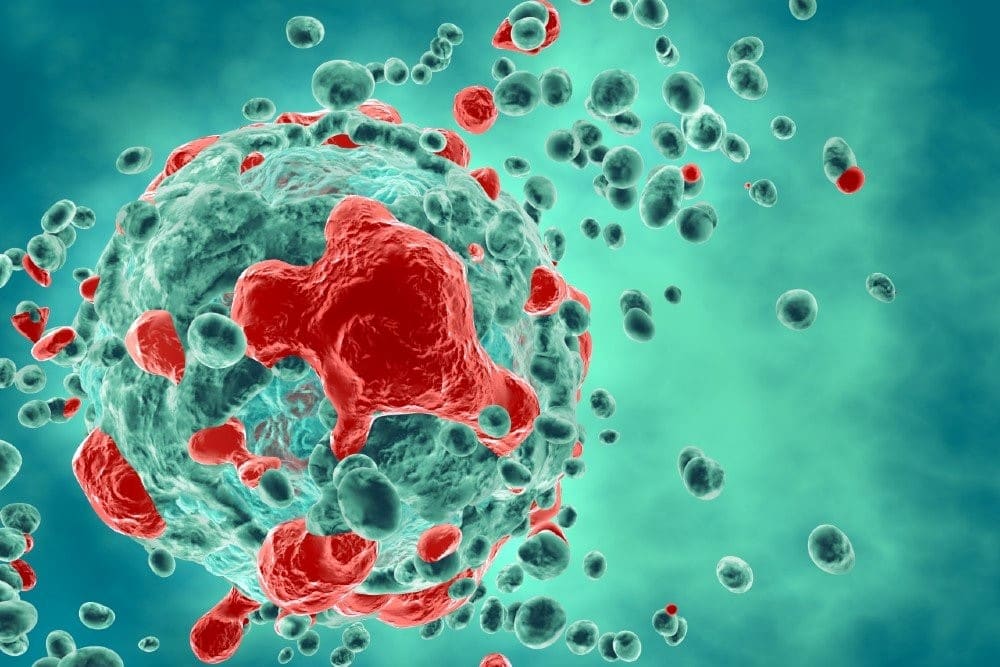
The customer developed a lab bench microfluidic system for automated microfluidic drug screening on cells cultured on a microfluidic chip dedicated to research use. The system consisted of several components, including custom-made microfluidic cards, pressure source, pressure-based flow controllers, and microfluidic valves for automated fluidic handling and parallelization.
As this ground-breaking microfluidic system provides many benefits compared to existing laboratory automation, the group of researchers launched their own company to provide a solution based on their microfluidic system.
The main challenge the group faced was to start from a multi-component lab bench system that is not suited for the industry (lengthy training, unoptimized process times, robustness, and a large footprint) and obtain a compact, user-friendly, and optimized device that is more user friendly with automation capabilities for microfluidic drug screening.
The group collaborated with Fluigent to design and build a custom system that meets their customers needs.
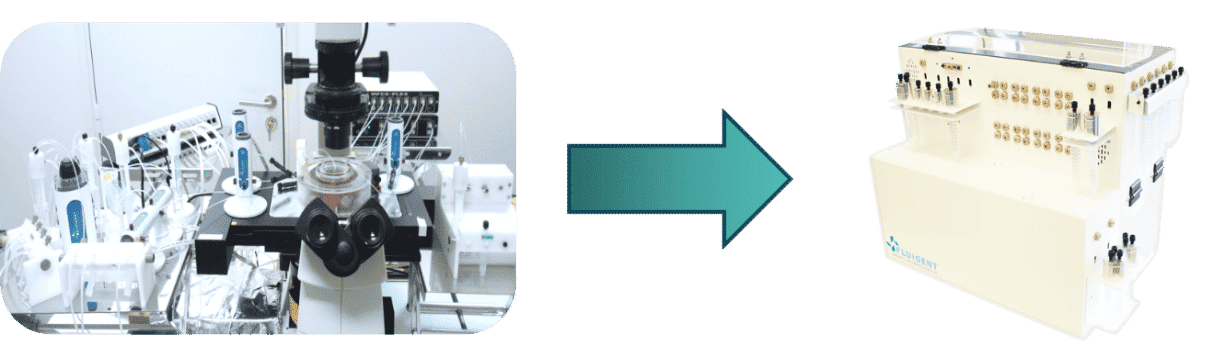
Fluigent expertise for industrializing your automated microfluidic solution
In collaboration with the client, Fluigent’s engineering team helped to create a compact, turnkey solution while meeting all bio-chemical specifications.
- Mechanical integration: Bubble formation is a known challenge in the microflow regime. Fluigent experts consider reliability risks when designing the fluidic architecture, for example, to minimize risks of bubble formation and allow the operator to focus fully on their application.
- Software integration: Integrating various components in a centrally controlled system comes with the challenges of operating multiple firmwares simultaneously. Fluigent software capabilities helped integrate non-fluidic components (optical instrumentation) to communicate with the machine control systems.