Creating Microcapsules With PEGDA Hydrogel
In this application note, the UV-crosslinked microcapsule production platform was used to produce single or double emulsions to form monodisperse Poly(ethylene glycol) diacrylate (PEGDA) microparticles or microcapsules. This note discusses how to choose the correct photoinitiators, to add PEGDA hydrogels to initiate a crosslinking reaction under UV irradiation, and their effect on the microparticle characteristics.
The RayDrop, developed and manufactured by Secoya Technologies, is used in this application note.
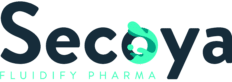
Characteristics and Advantages of Using PEGDA for Biomedical Applications
PEGDA hydrogel is a promising material for applications in the biomedical field, most notably in drug delivery and tissue engineering. [1] Its composition of polyethylene glycol molecules linked to diacrylate groups offers biocompatibility and adaptability. When exposed to UV light, the PEGDA polymer when coupled with a photoinitiator leads to crosslinking, forming a solid structure. This structure has similarities to the properties of biological tissues, making it ideal for use in the following ways:
– Protection from active pharmaceutical ingredient degradation (API).
– Control of active substance delivery releasing the contents of the microparticle or capsule in a specific area. [2]
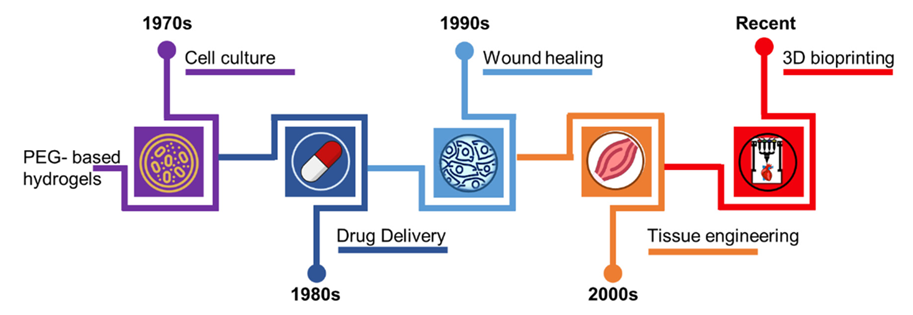
Figure 1: An overview of the use of PEG-based hydrogels in biomedical and biological applications [3]
Microfluidics: An Efficient Tool for Microparticle Synthesis
Classical methods of microparticle or microcapsule production, such as coacervation, spray drying, and solvent evaporation, require complex processes and equipment, making it difficult to control the size and encapsulation. Microfluidics enables monodisperse emulsions, resulting in microcapsules with highly controlled size and structure. With this approach, it is possible to create capsules of various compositions, allowing for the encapsulation of both polar and non-polar phases. Aqueous phases can contain proteins or APIs, while hydrophobic phases can encapsulate lipophilic or poorly water-soluble drugs.
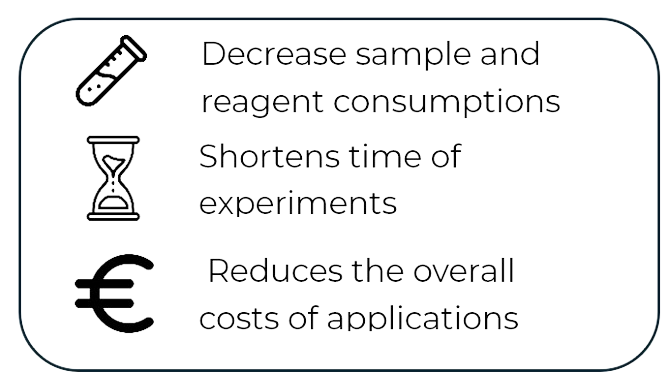
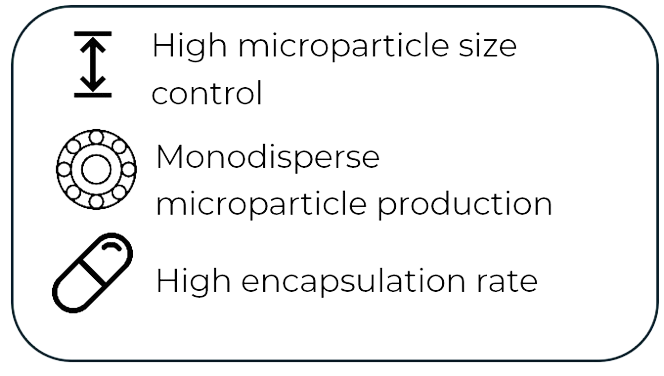
Figure 2: Advantages of microfluidic droplet.
All-in-One and Ready-to-Use System for UV-Crosslinked Microcapsules Production
The platform combines Secoya Technologies’ experience in droplet generation with Fluigent’s fluid handling knowledge to offer a state-of-the-art and easy-to-use microparticle formation.
The system incorporates the RayDrop (Secoya Technologies), which can produce both single or double emulsions. The microfluidic device’s geometry eliminates the need for surface treatments as the droplets are surrounded by the continuous phase and do not contact the capillary walls.
Fluigent Flow Controllers and Flow Units ensure precise flow control, stability, and responsiveness, which provides the ability to control microcapsule formation parameters. The system integrates microfluidic, mechanical, optical, and UV modules, offering a user-friendly, efficient, and versatile solution for PEGDA hydrogel microcapsule production.
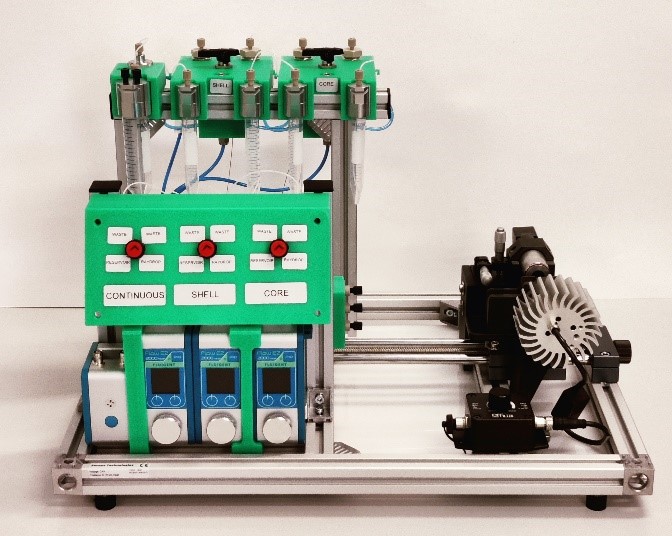
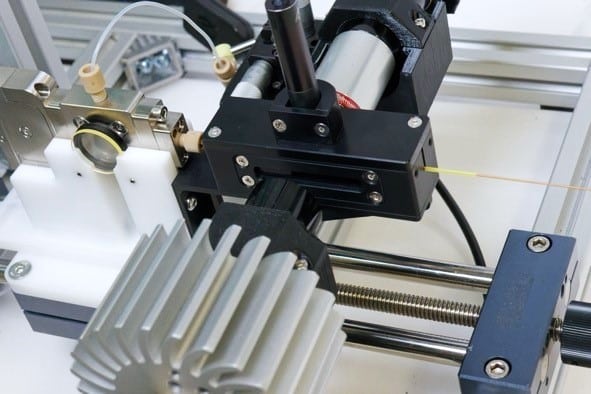
Figure 3: UV-crosslinked platform and its UV module.
How to Form PEGDA Microcapsules and Microbeads
In this application note, microbeads and microcapsules were produced using PEGDA-250 as it is insoluble in water, unlike PEGDA-575 or PEGDA-700. Three photoinitiators (DORACUR 1173, DORACUR TPO, or IRGACURE 2959) were tested and studied to demonstrate their influence on the microcapsule’s characteristics.
Experiments:
PEGDA hydrogel microcapsules were produced by following these steps:
- The RayDrop was filled with the continuous phase.
- The continuous phase was fixed to the desired flow rate.
- The shell priming and cleaning phase were added to produce the first emulsion.
- The core phase was added, generating a second emulsion.
- When flow rates were stable, the shell priming phase was switched with the shell phase (PEGDA solution) (figure 4).
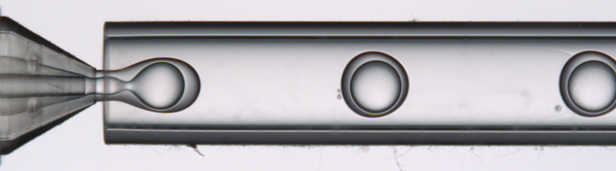
Figure 4: Generation of droplets using the RayDrop.
The droplets were passed through the UV module, which is plugged at the exit of the RayDrop and permits the instant polymerization of the PEGDA hydrogel microparticles or microcapsules (UV lamp irradiated at 385 nm) (figure 5).
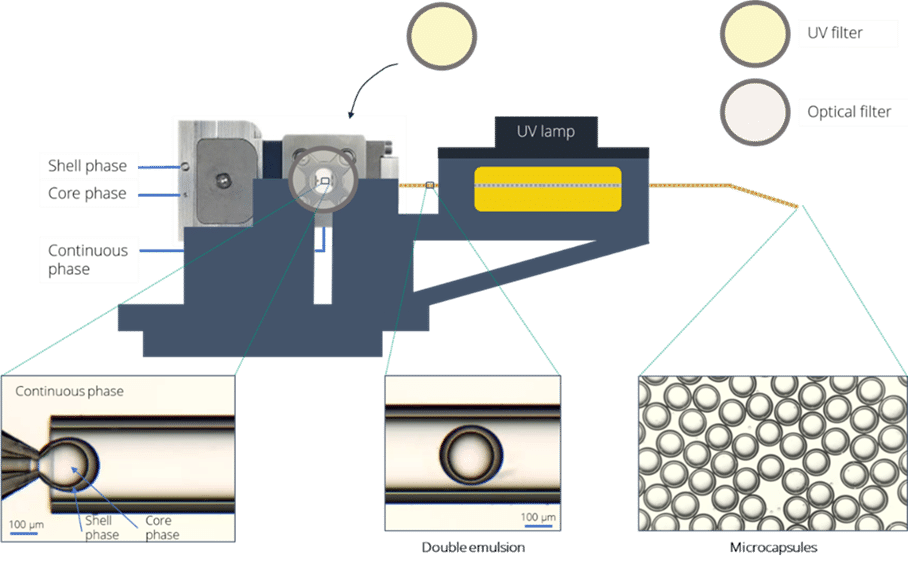
Figure 5: UV module In-situ cross-linking process leads to the formation of monodispersed microcapsules.
Partial results
When exposed to a UV source (wavelength: 385 nm, and minimum intensity Imin: 3.8 mW/cm²), TPO presented the best compatibility with PEGDA polymers as stable and monodispersed capsules were produced using the platform (figure 6). Under the same conditions, the capsules, formed while using DORACUR 1173 or IRGACURE 2959, were not stable and the shell became unstable within 1 minute of formation.
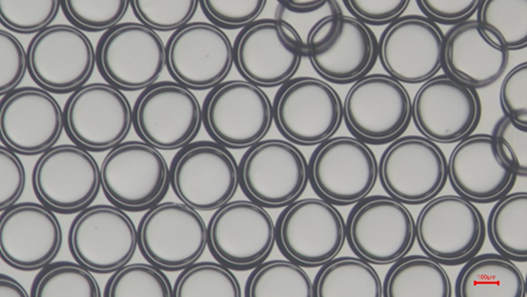
Figure 6: PEGDA particles with TPO photoinitiator. The scale bar corresponds to 100µm.
The mechanism between the TPO photoinitiator and the PEGDA hydrogel can be explained in Figure 7. The photoinitiator reacts to the light and initiates cross-linking of the PEGDA. A chain-growth mechanism is enabled, leading to the formation of a three-dimensional structure.

Figure 7: Chain-growth mechanism using TPO photoinitiator.
The interaction between the PEGDA hydrogel and TPO creates rigid shell microcapsules. To break them, an external force is required, such as a mechanical force applied by tweezers (figure 8).
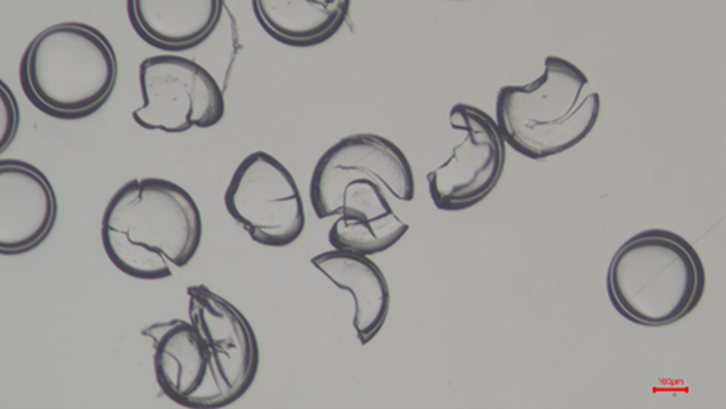
Figure 8: Broken PEGDA capsules using tweezers. The scale bar corresponds to 100µm.
Conclusion
This application note demonstrates the ease of producing PEGDA beads and capsules using the all-in-one UV -crosslinked microcapsule production platform. The study compares three different photoinitiators, highlighting their impact on the robustness of the final particles. The TPO photoinitiator is recommended due to its compatibility with PEGDA hydrogel, matching irradiation length with the UV lamp used, and fast kinetics, resulting in quickly formed, rigid beads and capsules.
Webinar: Controlled UV-crosslinked microcapsule production using microfluidic technology
Learn how to use the double emulsion platform to create microcapsules with PEGDA hydrogels.