Encapsulation of multiple emulsions in a single droplet
The objective of this application note is to describe the encapsulation of multiple aqueous “core” droplets inside a single oil droplet called a “shell”. To perform encapsulation of multiple emulsions, we used two Raydrop devices, and a capillary-based microfluidic device equipped with a 3D printed injection nozzle, developed and manufactured by Secoya. The two devices, installed in series on the complex emulsion production platform, allow the encapsulation of multiple emulsions in a single droplet, with fine-tuning of size and number of encapsulated cores achieved by varying the flow-rates.
Secoya developed and manufactured the RayDrop used to perform this application note.
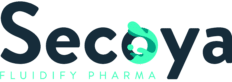
Introduction to multiple emulsion encapsulation
Limitations of traditional methods
Traditionally, multi-core double emulsions are produced using batch methods, with 2-step mixing of immiscible phases: a vigorous mixing step followed by a gentle one. This method is straightforward and allows for production of large batches, but is limited by a wide size distribution. This leads to a large number of particle sizes and a low encapsulation rate of Active Pharmaceutical Ingredient (API) or double emulsion production (core-shell particles).1
Microfluidics for encapsulation of multiple emulsions
Microfluidics emerged in the 2000s as a powerful tool to overcome the limitations of batch methods that offers fine control over the size, monodispersity, and structure of droplets.2 In particular, microfluidics is useful for generating complex emulsions such as water-in-oil-in-water (W/O/W) or oil-in-water-in-oil (O/W/O) emulsions.
Based on the work of Li, E. Q. et al,3 a new tool called the Raydrop with the ability to provide controlled encapsulation of multiple emulsions was demonstrated by the scientific experts at Secoya technologies. These devices enable multiple applications that create single and double emulsions, and are of particular interest for creating solid microcapsules for triggered release1 or to co-encapsulate incompatible and cross-reactive solutions.4
In this application note, we demonstrate that we can use two Raydrops connected in series to produce multi-core double emulsions with precise control over droplet number and size.
Generating multi-core double emulsions
Reagents
Core phase:
- 2% Tween20 (Sigma-Aldrich) in water
Shell phase:
- Mineral oil light containing 2% ABIL EM 90 (Evonik) and 0.08% Bromocresol Purple (Sigma-Aldrich).
Continuous phase:
- Solution of 70% wt glycerol (>99.5%, Sigma-Aldrich) in water with 2% Tween20 (Sigma-Aldrich)
Complex emulsion production platform
A fully integrated platform, developed by Secoya, was used to perform encapsulation of multiple emulsions. Mechanical, fluidics and optics modules are integrated to provide straightforward, user-friendly and controlled production of simple and double emulsions.
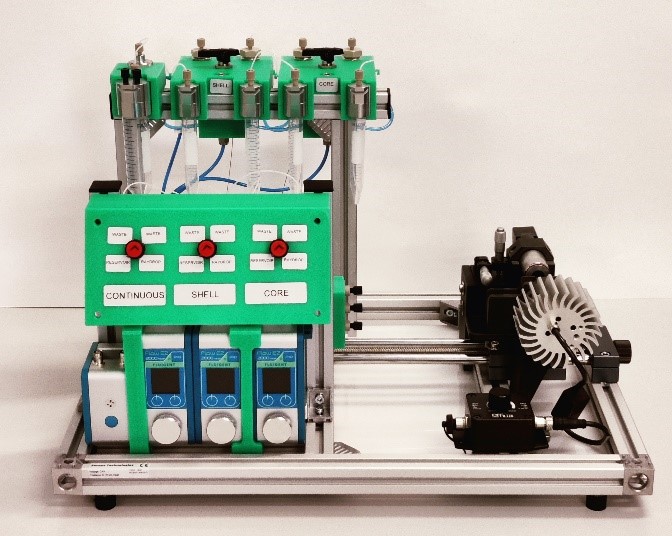
The experimental setup used for encapsulation of multiple emulsion is schematically represented in Figure 2. Here, a second RayDrop (R2) is placed next to the first RayDrop (R1).
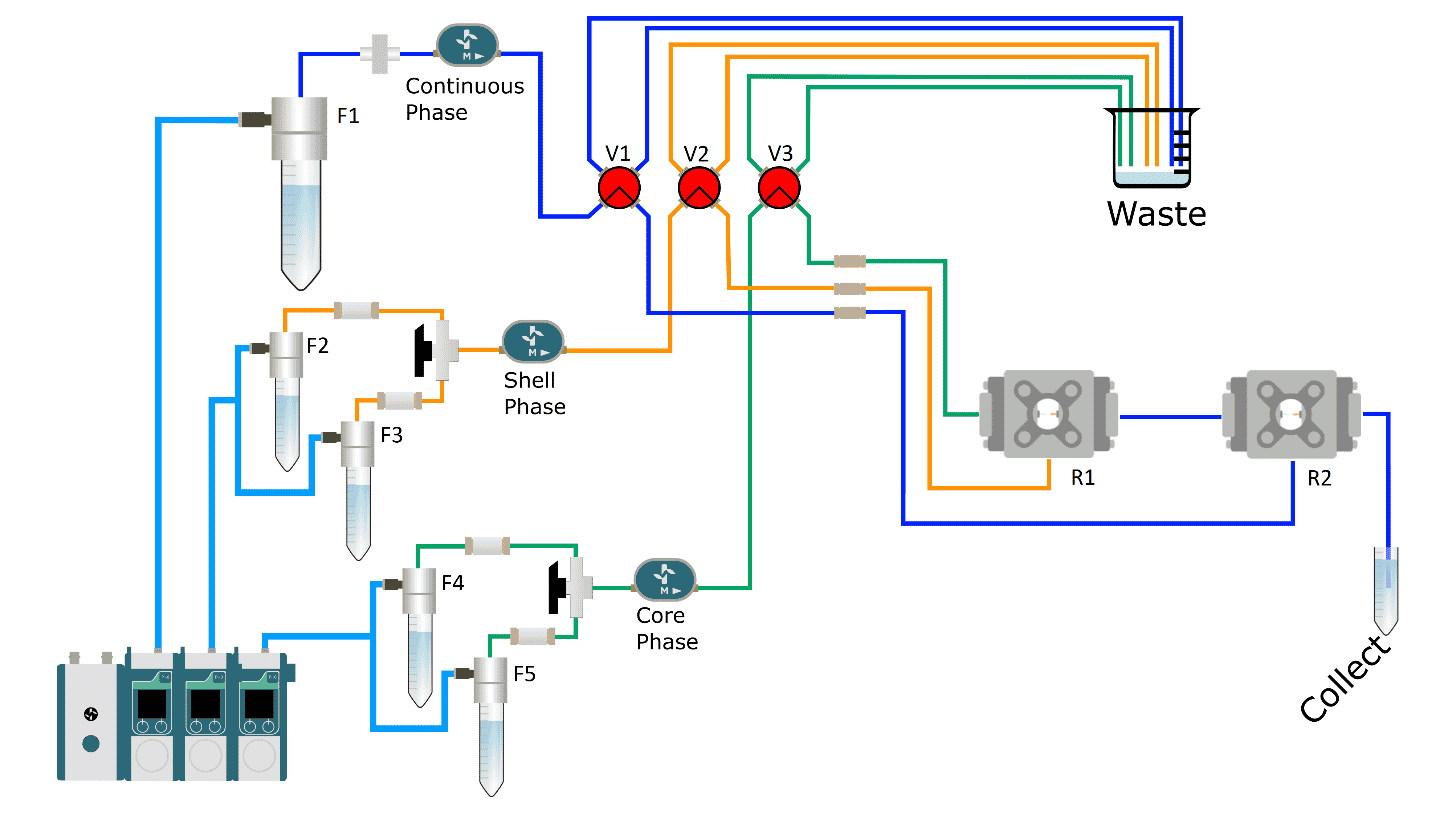
Fluid reservoirs
Reservoir | Volume (mL) | Phase | Composition |
F1 | 50 | Continuous | 70% glycerol + 30% water + 2% Tween 20 |
F2 | 25 | Shell (priming & cleaning) | Not used in this application note |
F3 | 25 | Shell | Mineral oil light + 2% ABIL 90 + 0.08% Bromocresol |
F4 | 25 | Core (priming & cleaning) | Not used in this application note |
F5 | 25 | Core | Water + 2% Tween 20 |
RayDrop design
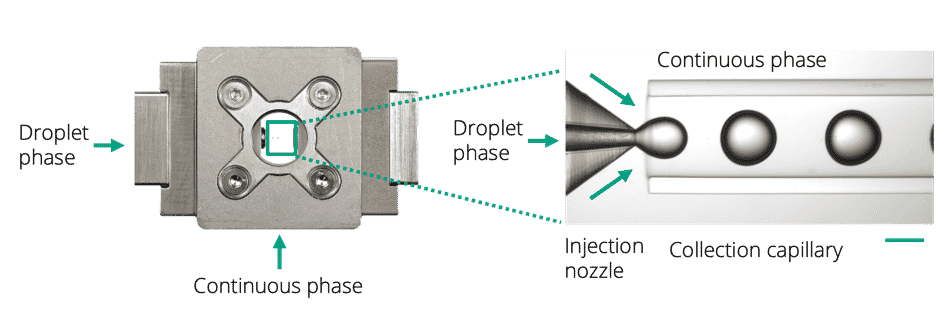
The RayDrop is a microfluidic droplet generator based on the alignment of two glass capillaries. The first capillary is terminated by a 3D printed nozzle and injects the droplet phase into the second one. At the junction of the two capillaries, the continuous phase filling the cavity pinches the jet of the droplet phase, leading to the formation of droplets with high monodispersity.
In this case, two RayDrop systems are arranged in series to perform encapsulation of multiple emulsions. A first device R1 is mounted on the platform as for simple emulsion generation, and a second Raydrop R2 is added immediately after (see figure 2). To efficiently control the formation of droplets inside the second RayDrop, an additional optical module (LED + camera) is placed on the platform.
The oil phase, containing the aqueous “core” droplets encapsulated in the R1 device, is transported as the “shell” phase (see Figure 4) towards the R2 device. Here, the oil phase is pinched by the continuous phase, which leads to the formation of monodisperse oil droplets, each containing multiple aqueous cores. The number of cores in each droplet can be controlled by tuning the flow-rates.
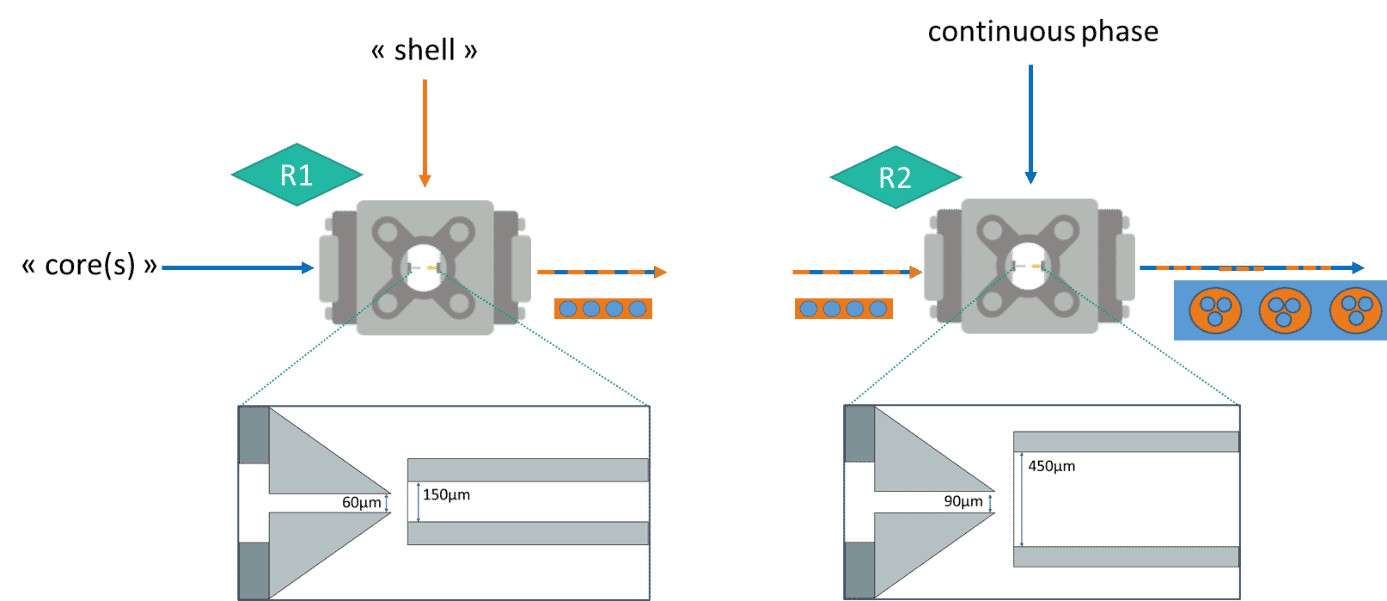
Figure 4: Two RayDrop placed in a series (their nozzle dimensions are displayed).
Nozzle information
The range of droplet sizes formed depends on the dimension of both the injection nozzle and the collection capillary. The dimensions used for the encapsulation of multiple emulsions in this application note are reported below.
Part | RayDrop | Nozzle size (µm) | Collection capillary size (µm) |
Inner diameter | 1 | 60 | 150 |
Inner diameter | 2 | 90 | 450 |
Table 1: Nozzle and collection capillary dimensions
Multiple emulsion generation
To perform reproducible and monodisperse encapsulation of multiple emulsions, the protocol below can be followed:
1. Set valve V2 on reservoir F3 containing the shell phase
2. Set valve V3 on reservoir F5 containing the core phase
3. Fill RayDrop R1 with the shell phase solution (refer to the user guide for more details on how to fill the RayDrop)
4. Fill RayDrop R2 with the continuous phase solution
5. Connect the two filled RayDrops together with the tubing
6. Carefully set the continuous phase to a low flow rate (e.g. Qcontinuous= 40µl/min) and check that there is no backflow in the first RayDrop.
7. Set the shell phase to a low flow rate (e.g. Qshell= 7µl/min with Qshell<Qcontinuous) to create a simple oil-in-water emulsion visible in the second RayDrop.
8. Set the core phase to a low flow rate (e.g. Qcore= 1µl/min) to generate simple emulsions in R1, which leads to the generation of multiple emulsions in R2.
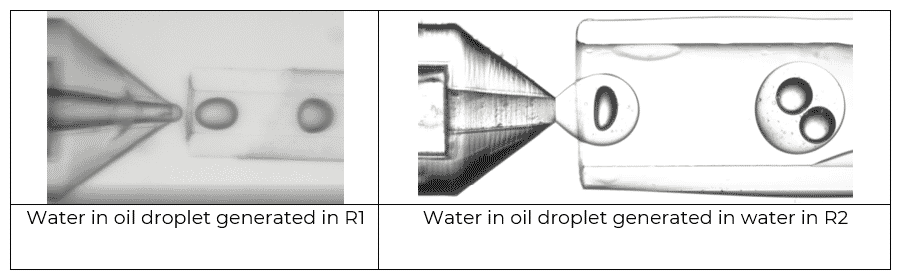
9. The encapsulation of multiple different emulsions in a single droplet is now in progress. The dripping mode provides high stability for droplet formation. Droplets show high monodispersity. It is possible to vary the flow rates in order to change the size of the emulsion as well as the number of cores (see the following section for more details).
Partial results
The number of cores in a single droplet depends on the flow rate of the core phase.
During the formation of the multi-core double emulsions in RayDrop R2, the flow rates of the shell and continuous phases are kept fixed. Therefore, only the flow rate of the core phase is changed. By increasing the core flow rate, the number of encapsulated core droplets also increases. For a core flow rate of 0.5µl/min, most droplets contain one core, while for a core flow rate of 2.3µl/min, most droplets contain four cores.
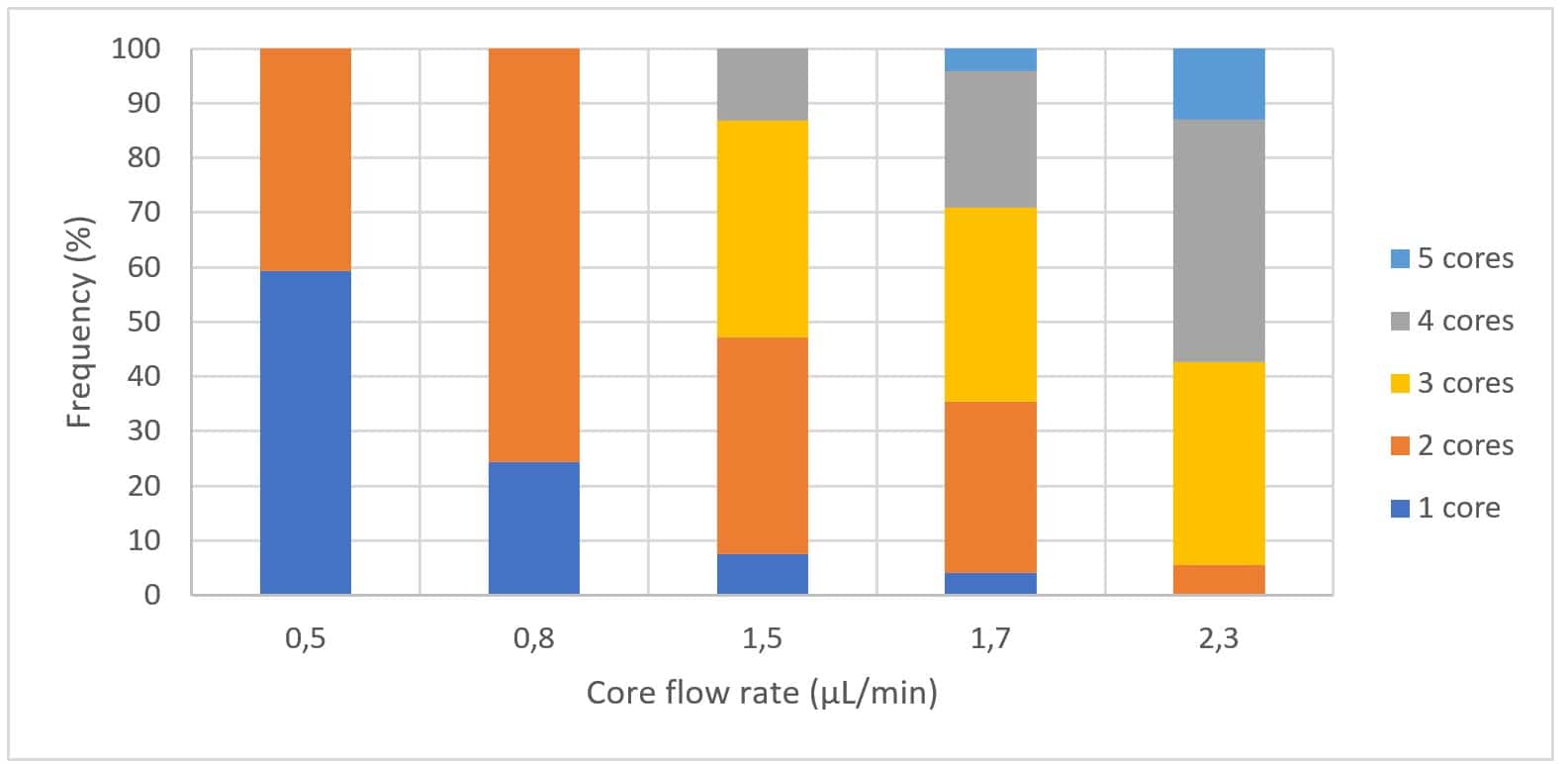
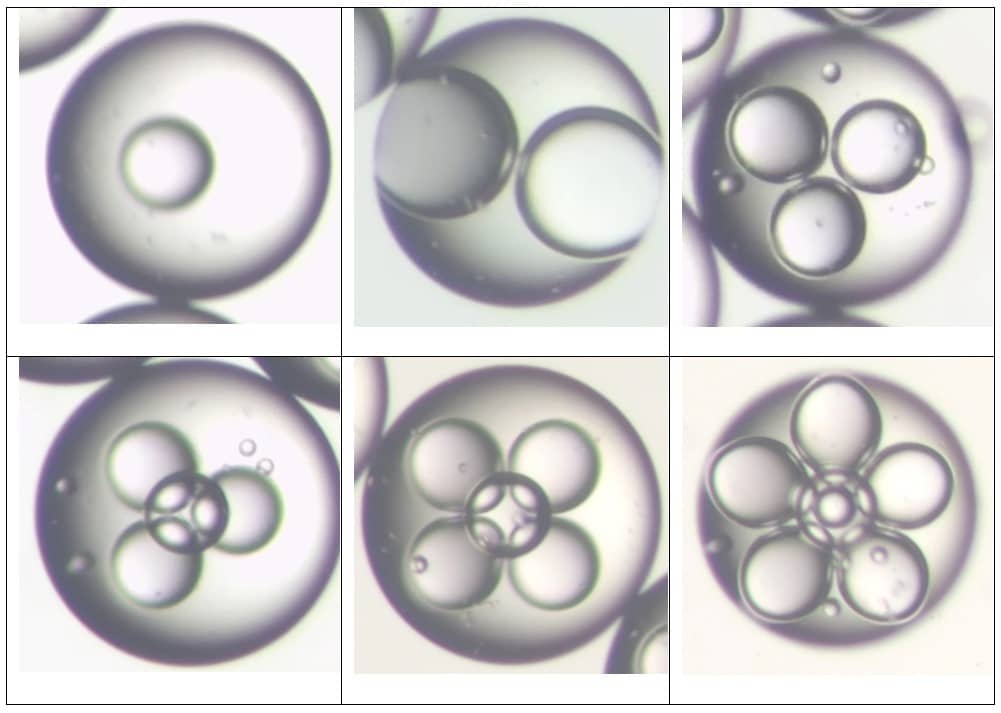
Conclusion & Perspectives
We demonstrated the possibility of making an encapsulation of multiple emulsions in a single shell by using two Raydrop devices in series on the complex emulsion production platform. By playing with the flow rates of the core phase, one can control the number of encapsulated cores. By combining the “two chips in series” platform structure with the use of a double emulsion Raydrop device, even more complex emulsions could be achieved, including multiple encapsulations of double emulsions in a single droplet.
Related content
Double emulsion production made easy: a reliable device
Read more- Microfluidic Application Notes
Double Emulsion Generation
Read more - Array
Master the production of Double Emulsions
Read more WEBINAR: Encapsulation of fluorescent bacteria in double emulsions for FACS sorting
Read more- Array
Drug encapsulation in biocompatible microparticles for drug delivery
Read more Workshop Encapsulation of active ingredient in microparticles and microcapsules
Read more
References
[1] Vladisavljević, G., al Nuumani, R. & Nabavi, S. Microfluidic Production of Multiple Emulsions. Micromachines (Basel) 8, 75 (2017).
[2] Lee, T. Y., Choi, T. M., Shim, T. S., Frijns, R. A. M. & Kim, S.-H. Microfluidic production of multiple emulsions and functional microcapsules. Lab on a Chip 16, 3415–3440 (2016).
[3] Li, E. Q., Zhang, J. M. & Thoroddsen, S. T. Simple and inexpensive microfluidic devices for the generation of monodisperse multiple emulsions. Journal of Micromechanics and Microengineering 24, 015019 (2014).
[4] Wang, W. et al. Controllable microfluidic production of multicomponent multiple emulsions. Lab on a Chip11, 1587 (2011).