Pressure predictions for lab-on-chip operations using a microfluidic network solver and Fluigent PX
Lab-on-chip applications require easy-to-use, accurate and predictable fluid handling solutions adapted to the different steps of the process and their respective sample fluids. Pressure-based flow control allows for excellent performance in terms of flow control, response time and range of flow rates.
In this application note, we report on the combination of Fluigent PX with a microfluidic network solver for highly accurate predicted pressures and millisecond response times.
This was possible thanks to Julia Sophie Böke, Daniel Kraus and Thomas Henkel from the Leibniz Institute of Photonic Technology in Jena (Germany).
Introduction to pressure prediction
Microfluidic flow protocols have evolved to allow multiple fluidic tasks to be integrated into a single device, making it increasingly important to ensure reliable flow control via excellent flow rate and operating pressure prediction. More precisely, predicting the pressures required to reach the desired flow rates with a given configuration and hydrodynamic resistance has become essential. To this end, “microfluidic design automation”1 tools have been developed. By defining resistive networks, it is possible to predict the flow rate within the microfluidic network (MFN).
We report the use of our pressure-based flow controller Fluigent PX for the development of a microfluidic platform managing fluids with a microfluidic network solver. The software is called mfnSolver. The platform allows for accurate prediction of pressure settings with excellent response time for operations at steady state. It also enables knowledge about on-chip pressure drop and flow characteristics to be gained. The microfluidic automated operations are demonstrated by making laminar co-flow of up to four components, and variable-composition droplets in several regimes (dripping, transition, jetting) from up to three components.
Predicting operating pressures with a microfluidic network solver
Materials & methods
Microfluidic flow control
- Pressure-based flow controller: Fluigent PX 1 bar. The quality of set and display pressure are shown below.
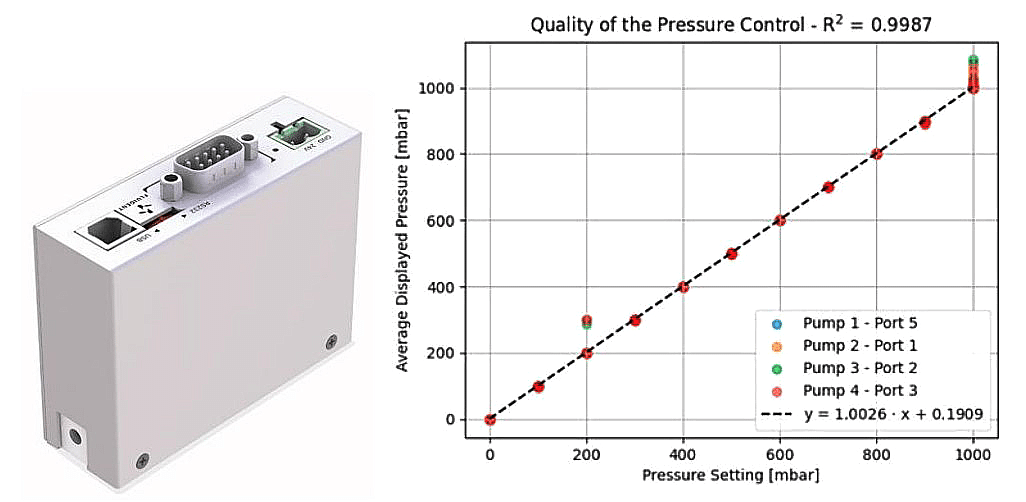
- Reservoirs: Fluiwell-4C 2 mL vials screwed to the rack for pressure connection.
- Flow sensors: Fluigent Flow Unit M (0 – 80 µL/min).
- Flow control software: Fluigent A-i-O software (now OxyGen).
Microfluidic chip:
- Chip: flow-focusing unit (FFU) of the Leibniz-IPHT PDG2 Droplet Generator Chip (PDG2). The PDG2 chip has 4 inlets (P1, P2, P3, P5) and 1 outlet (P4)1.
- Channel width: 165 µm before the flow focusing region, 200 µm at the observation chamber, and 150 µm otherwise – Channel height: 100 µm.
- Surface treatment (for droplet generation): PlusOne Repel-Silane ES (solution of Dimethyldichlorosilane (2% w/v) in Octamethylcyclotetrasiloxane).
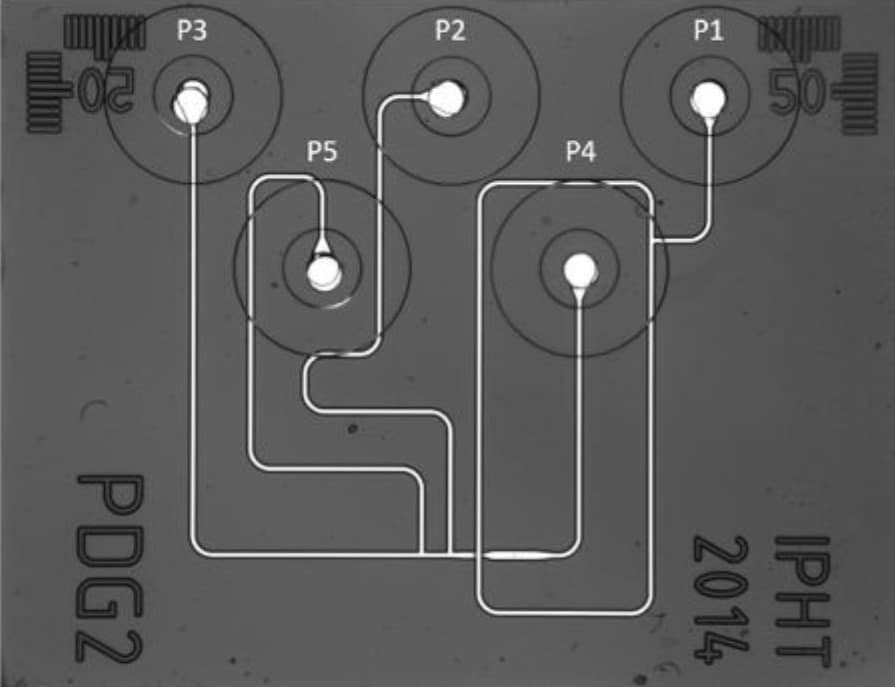
Buffer and Reagents:
• Dye solutions: 2 mmol/L Bromophenol blue solution (Sigma-Aldrich) for which 13 mg of the sodium salt dye was dissolved in 10 mL sodium phosphate buffer – 4.9 mmol/L Orange G solution containing 22 mg disodium salt dye in a 10 mL buffer
• Surfactant for droplet generation: Fluigent dSurf (2% surfactant in Novec™ 7500)
mfnSolver:
The microfluidic network solver developed by Böke et al. gives the pressure and flow rate at all defined nodes and edges of the chip1. It can solve a complete microfluidic system in less than 200ms. The user only has to define the flow rates along arbitrary edges of the network for the solver to compute the differential pressure required to reach them. In addition, the mfnSolver can help users to design and optimize microfluidic components, predict network performance, and automate the operation of devices based on pressure-driven fluid management.
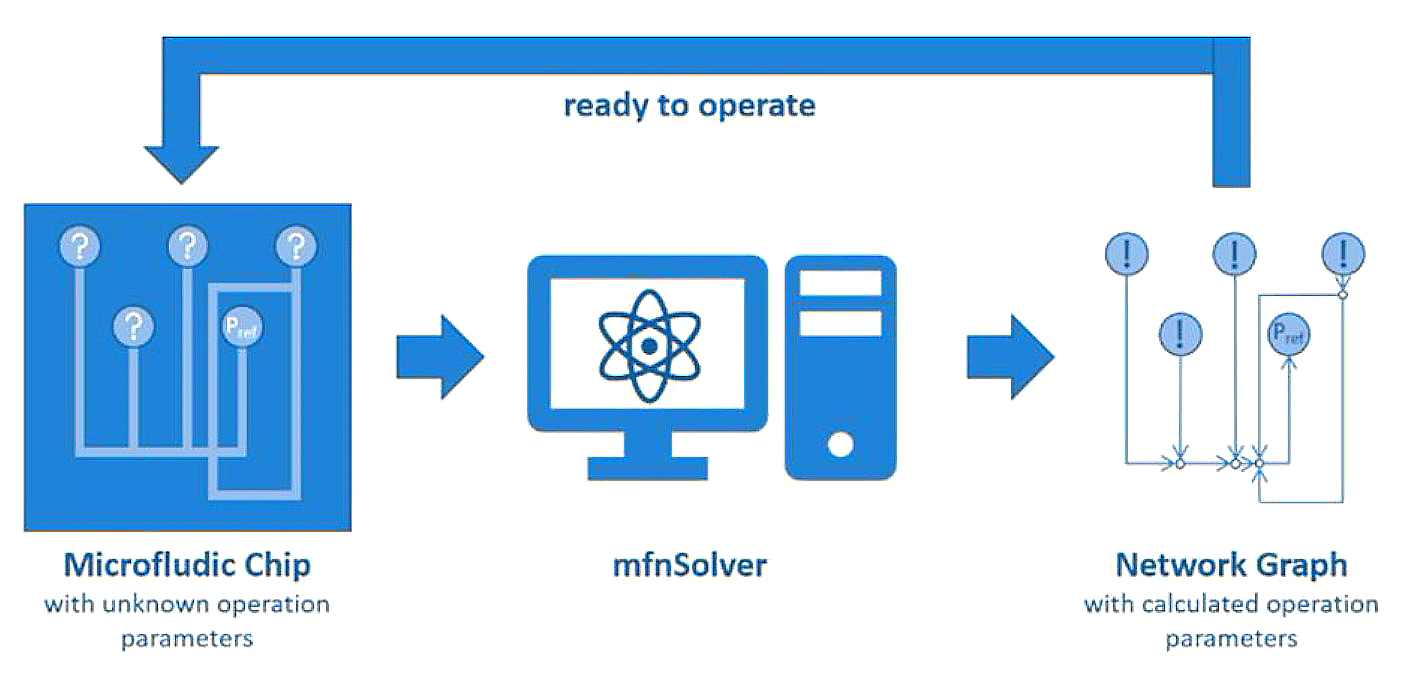
Partial results
Microfluidic system implementation:
The output prediction for a standard flow rate of 0.16 µL/min is shown in Figure 2. The microfluidic network solver gives the predicted pressure that corresponds to the input operating pressure for experimental validation.

Experimental validation:
Fluigent flow sensors are integrated into the fluidic feedline to monitor the flow rate during the experiment set to confirm the predicted flow characteristics.
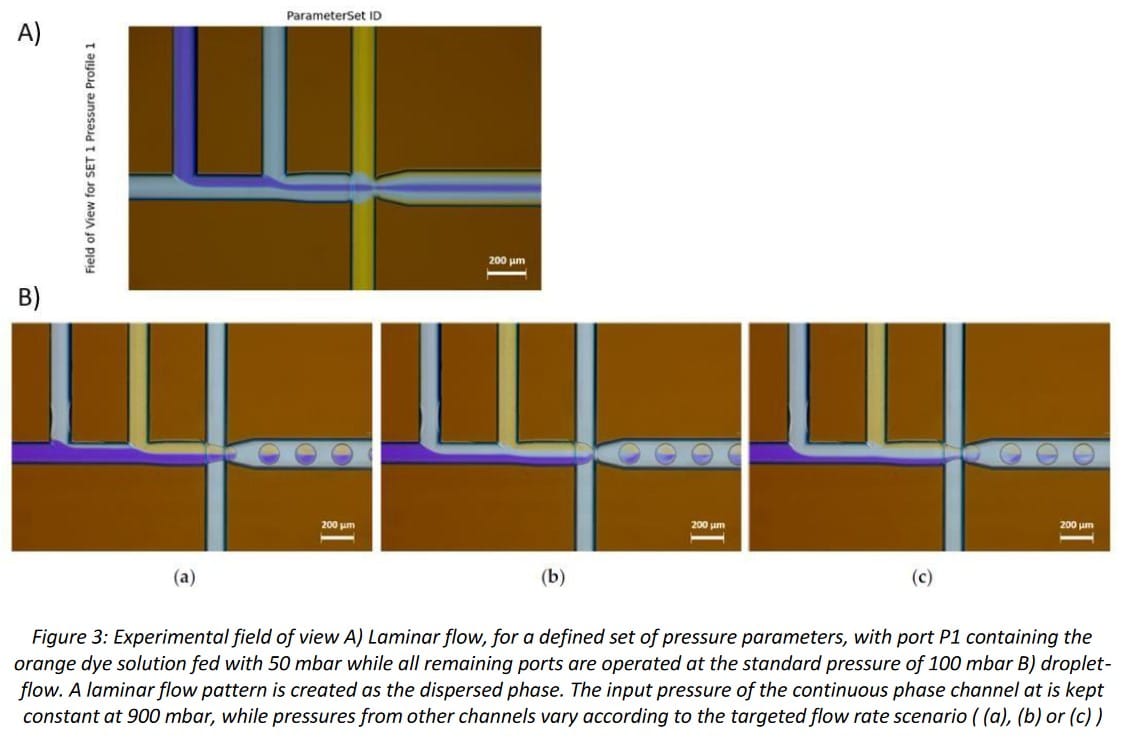
The graphs in Figure 4 display the comparison between the flow rate predictions according to the input pressure and the experimental results provided by the flow meter for laminar co-flow and droplet flow.
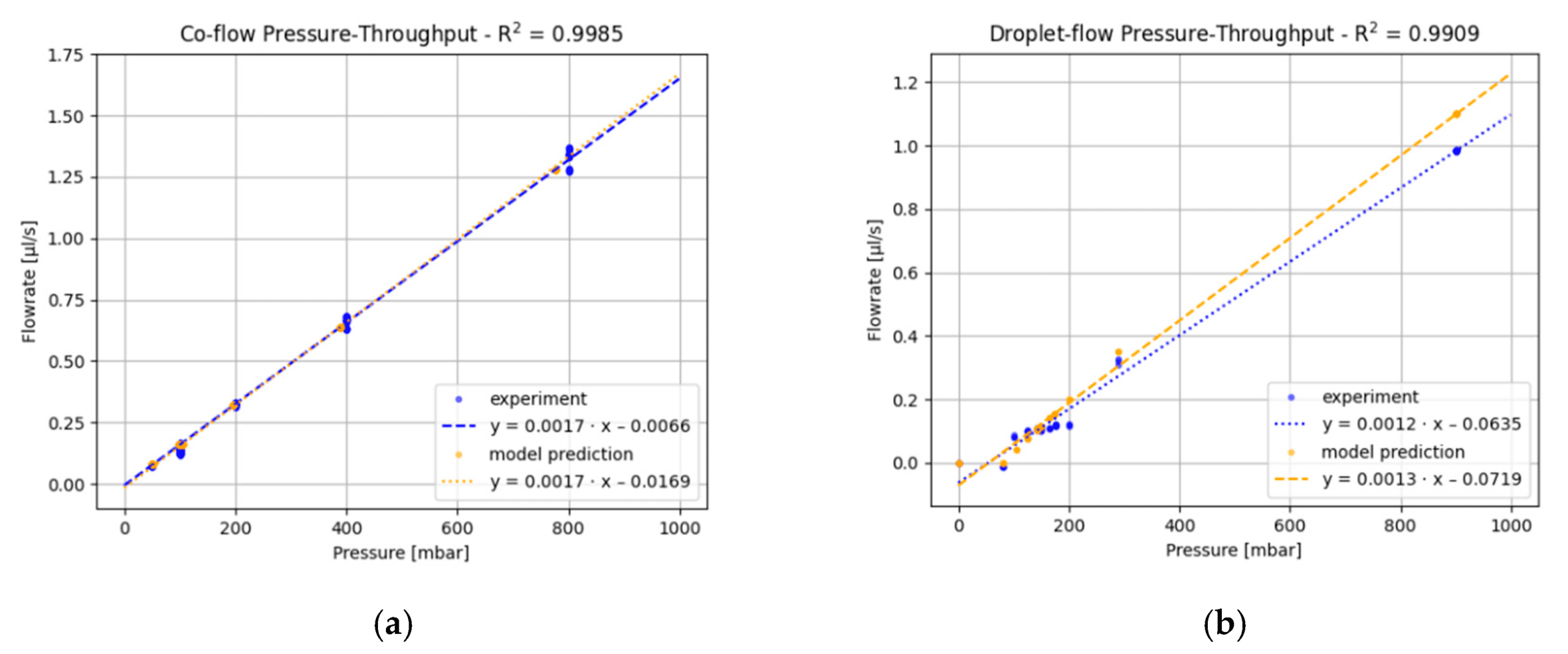
Conclusion
In this application note, we have reported that the microfluidic network solver mfnSolver is a tool for reliable and easy lab-on-chip operations, thanks to its fast and accurate operating pressure predictions at steady state and its support in obtaining information about on-chip pressure drop and flow characteristics.
With the growing complexity of microfluidic setups, the automation of fluid management is becoming a non-negligeable advantage. Fluigent PX helped in the development of this flow automation project as a solution to provide flows with excellent accuracy and response time.
Related product
Related content
5 reasons to choose OEM pressure controllers over OEM syringe pumps for microfluidic applications
Read moreContamination-free Liquid Handling System
Read more- Expert Reviews: Basics of Microfluidics
Key reliability indicators for OEM components to ensure long-term performance of your flow control system
Read more - Expert Reviews: Basics of Microfluidics
Key considerations for fluidic system integration
Read more
References
- Böke, J. S., Kraus, D. & Henkel, T. Microfluidic Network Simulations Enable On-Demand Prediction of Control Parameters for Operating Lab-on-a-Chip-Devices. Processes 9, 1320 (2021).