All-in-one and ready-to-use system
UV-crosslinked microcapsule production platform
- New release
An all-in-one platform for continuous generation of UV-cured core-shell microcapsules
The UV-crosslinked microcapsule production platform, developed and manufactured by Secoya Technologies, is a complete system for the continuous creation of core-shell microcapsules with control over size and structure.
Based on a droplet microfluidic approach, Secoya Technologies’ RayDrop device produces monodisperse double emulsions which lead to monodispersed microcapsules, while Fluigent’s Flow controllers and Flow Units guarantee high flow stability and responsiveness. Microfluidic, mechanical, optical, and UV modules are all included in the platform for easy, fast, and practical usage.
With its precise size and structure, UV-crosslinked microcapsules (for instance methacrylate-based resins, PEGDA, or PEGDMA) produced by the platform are used in life science applications for drug delivery, tissue engineering, crystallization, and more.
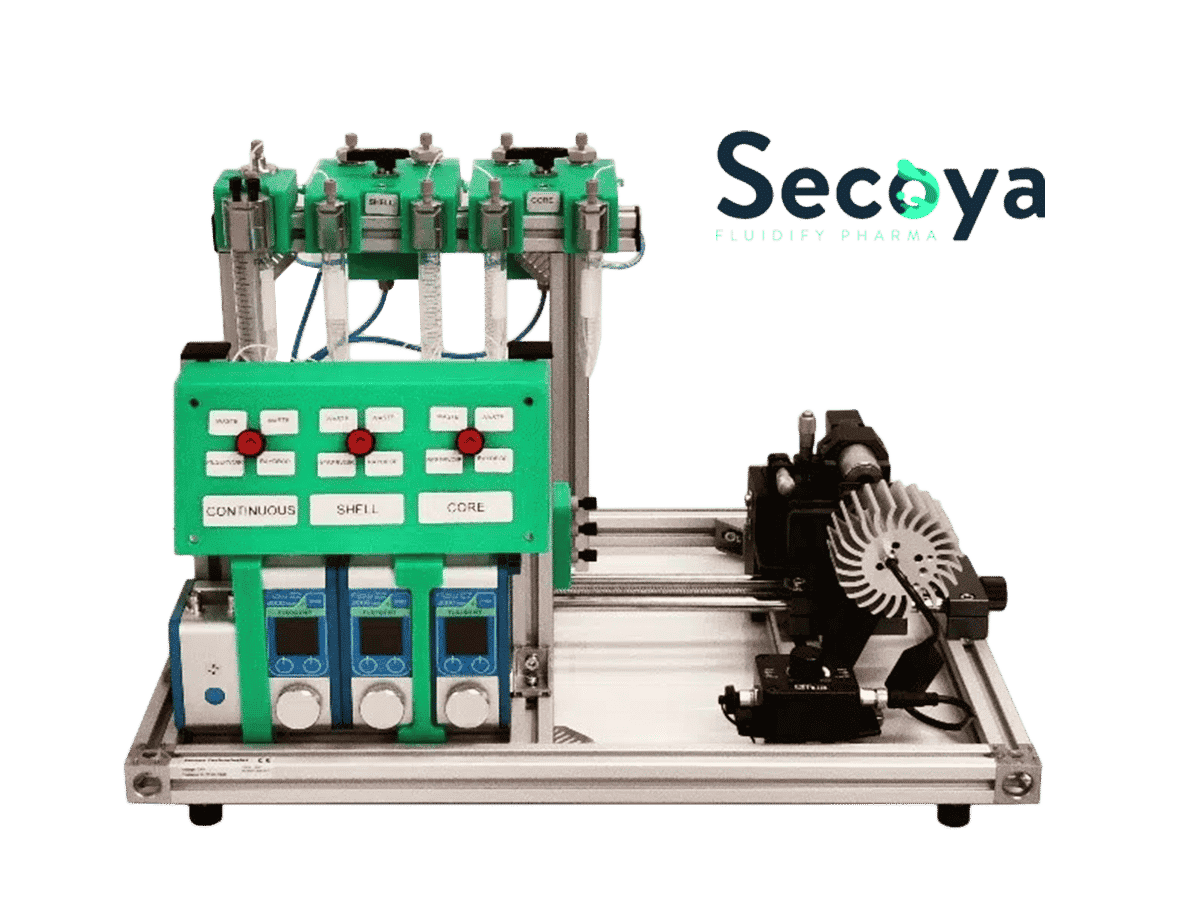
- Easy to use
- Practical
Direct UV-crosslinking and continuous production
- Provides High Control
Adjustable droplet size and shell thickness
- Guarantees High Precision
Down to 2% monodispersity
Features of the UV-crosslinked microcapsules production platform
Fluigent and Secoya’s Precision and Flexibility
Achieve precise emulsion generation with Fluigent’s advanced pressure-based flow controllers and Secoya’s RayDrop device. This technology enables the platform to create robust and monodispersed emulsions, allowing for accurate control over droplet size and shell thickness.
Streamlined and User-Friendly Engineered Solution
A fully equipped, mounted, and meticulously controlled tool designed for direct microcapsule production, with easy priming and cleaning processes. Benefit from specialized optics tailored for superior droplet visualization at high frequencies, ensuring optimized results.
In-situ UV crosslinking process
Experience easy monitoring of emulsion formation with the UV movable module. Equipped with anti-UV glass windows, it ensures safe experimentation. UV light source (365 nm) initiates polymer cross-linking, resulting in solid capsules. With adjustable tubing inclination, the collection is simplified. The in-situ cross-linking process prevents coalescence, ensuring superior results.
UV-crosslinked microcapsules as a versatile tool in research
Core-shell microcapsules have emerged as pivotal tools in the pharmaceutical, cosmetic, and food industries for material delivery and release. In pharmaceutics, there’s a growing interest in encapsulating drugs, nutrients, and living cells within solid biocompatible shells to precisely target specific sites, driving intensive research efforts. As another type of application, microcapsules can be used as independent crystallization vessels for both small molecules and macromolecules such as proteins, salts, and chemical materials, affording scientists both low-scale experiments and screening capacities for the characterization of novel compounds, including screening polymorphism.

Schematic of core-shell microcapsules for drug delivery (From Ahmad, S. U. et al., Vet Pharm & Therapeutics 2021, 44 (3), 298–312.)
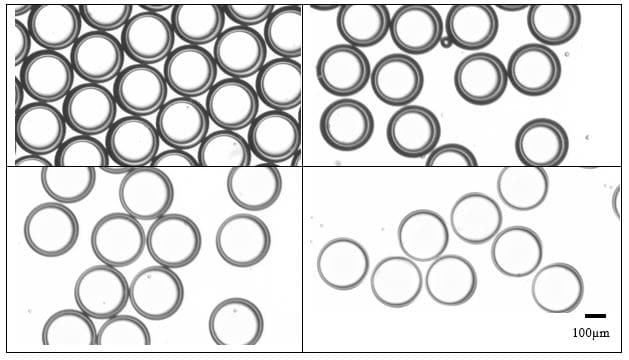
Microcapsule of 250µm with shell thickness adjustment between 10µm to 50µm.
However, classical microencapsulation methods like coacervation, spray drying, and solvent evaporation require complex processes and equipment, posing challenges in controlling microcapsule size and load.
Microfluidics offers a new approach, enabling the production of monodisperse double emulsions that yield uniformly sized microcapsules with precise control over structure. This technology allows for the easy encapsulation of aqueous solutions containing proteins or active pharmaceutical ingredients (APIs), as well as oily solutions containing lipophilic or poorly water-soluble drugs.
To transform the produced double emulsions into capsules, various methods of shell curing can be used depending on the shell nature such as solvent evaporation or precipitation (for PLGA capsules), ionic crosslinking (for alginate capsules), or chemical cross-linking (for chitosan capsules). Most frequently, UV light crosslinking (for PEGDA capsules) is used to produce polymeric capsules as it has the advantage of being solvent-free and is rapid compared to other curing methods.
How to use the platform to produce UV-crosslinked microcapsules
The platform is comprised of four main components: mechanics, fluidics, optics, and a UV module.
- Mechanics: It features x-y-z displacement plates to adjust focus and observation windows embedded in the RayDrop device.
- Fluidics: This includes flowrate controllers, tubing, valves, Falcon reservoirs, and the RayDrop for automated fluid injection. Filters are incorporated after each reservoir to eliminate impurities that could affect the RayDrop. The core phase can also be injected through an injection loop for encapsulation.
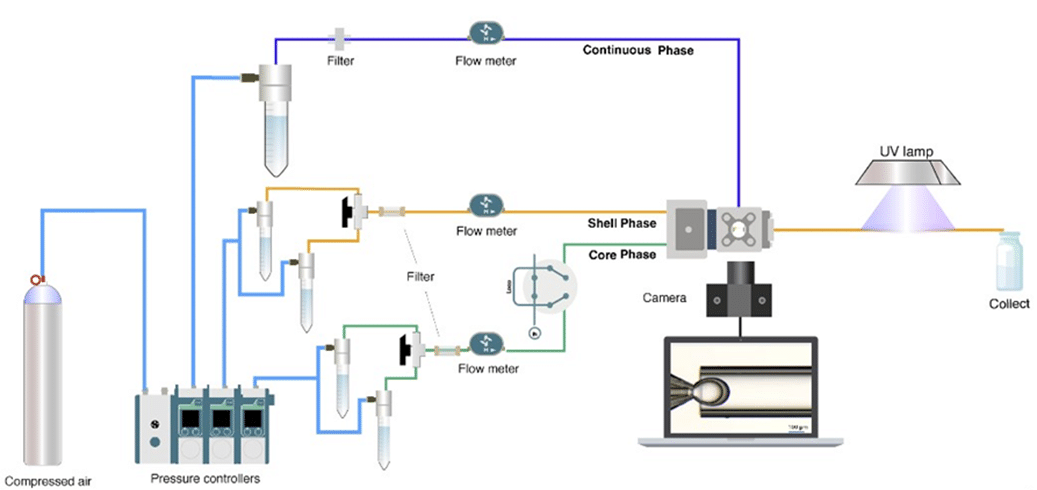
Experimental set-up to produce double emulsions. It includes double reservoirs for the shell and core phases and an injection loop.
The RayDrop utilizes emulsification technology to produce controlled double emulsions, typically stabilized with surfactants.
Nozzle information:
Part | Core nozzle | Size-shell nozzle | Size-extraction capillary |
---|---|---|---|
Inside diameter (µm) | 90 | 160 | 450 |
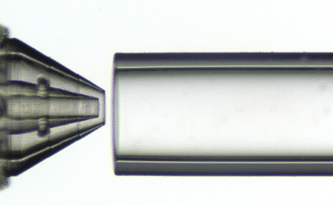
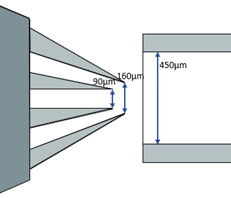
- Optics: The optical section consists of an LED light source and a color USB 3.0 camera connected to a computer for live observation of droplet formation, emulsion stability control, and size measurement.
- UV module: The UV module section creates mobility via a displacement plate for observing emulsion formation and stability at the RayDrop exit. Two windows with anti-UV glass ensure safe observation. A UV light source at 365nm initiates resin cross-linking in the tubing, resulting in hard-shell capsules, which can be collected in a vial with adjustable tubing inclination.
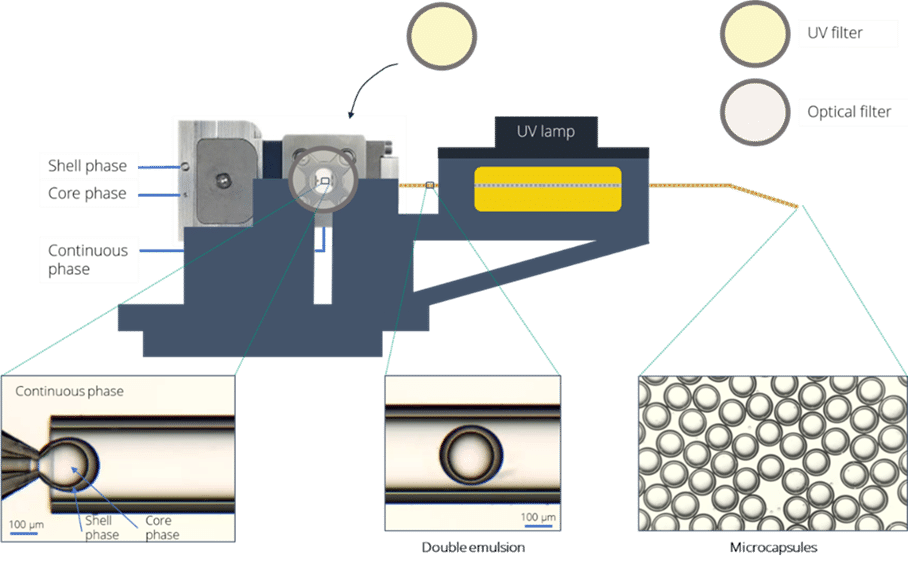
Example of Use: Production of UV-crosslinked microcapsules for crystallization
Based on the publication: Single crystal formation in core-shell capsules, M. Mettler et al., Chemical communications 2023
In this application example, the scope of microfluidic-based crystallization methods is extended by introducing solid microcapsules.
Hundreds of identical microcapsules were generated per second, creating a fast screening of crystallization conditions.
XRD analyses were performed directly on encapsulated single crystals, demonstrating the potential of this process for the identification of compounds.
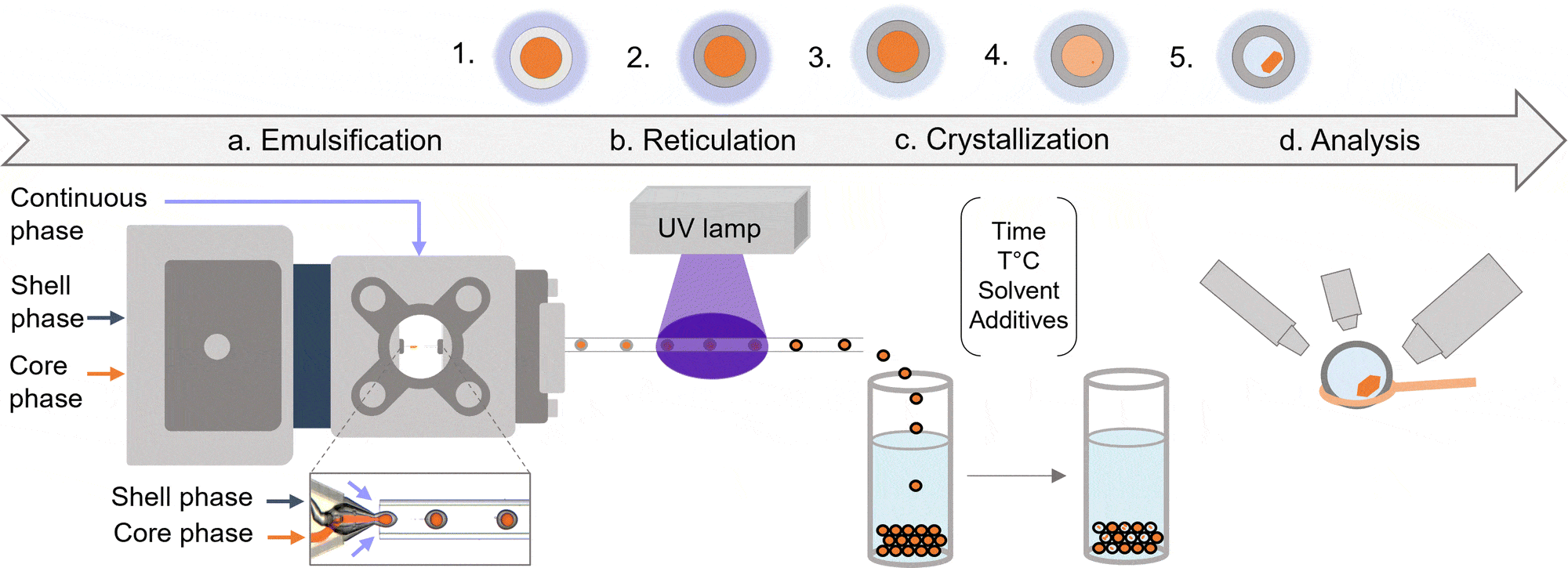
Schematic representation of the process from double emulsion generation to crystal formation and analysis in microcapsule. (M. Mettler et al., Chem. Commun., 2023, 59, 12739–12742)
Reagents:
- Continuous phase: Distilled water containing 2% Poly (vinyl alcohol) (PVA)
- Shell phase: Commercial Allnex methacrylate-based resin containing 20% of ethyl acetate) and 0.1% wt of photoinitiator Diphenyl(2,4,6-trimethylbenzoyl) phosphine oxide (TPO).
- Core phase: Distilled water with the molecule to crystallize (ammonium sulfate, copper (II) sulfate, glycerol, glycine, sodium chloride, proteinase K, or lysozyme).
Brief Protocol:
To generate a double emulsion, the system must first be primed with pure solvent in the shell phase. Once droplet formation is stable, the shell phase is switched to the methacrylate solution. This helps avoid clogging issues during the transient phase.
To form solid particles, the generated emulsion is irradiated by UV light. The photoinitiator reacts to the light and initiates a cross-linking with the methacrylate-based shell. A chain-growth mechanism is enabled, leading to a three-dimensional network.
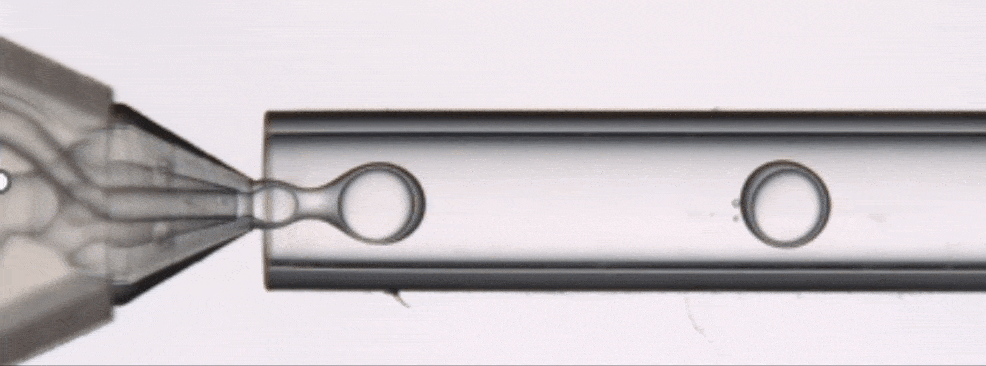
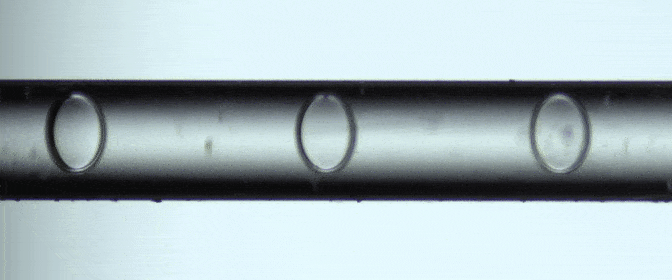
Key Benefits and results:
- Tailored Control: Adjust flow rates of continuous, shell, and core phases to control double emulsion size and shell thickness, ensuring precise experimentation.
- Mechanically Stable Capsules: Produced capsules are mechanically stable, allowing for easy handling and transport, ideal for in-situ crystal analysis.
- High Throughput Screening: Produces hundreds of capsules per second, each serving as independent crystallization vessels for various molecules, enabling efficient condition screening.
- Adaptable Configuration: Customize capsule size by modifying the RayDrop’s configuration, giving user’s experimentation flexibility.
- Versatile Application: Extend this approach to encapsulate various compounds and shell polymers, expanding your research possibilities.
- Unlock the potential of the RayDrop for your crystallization experiments.
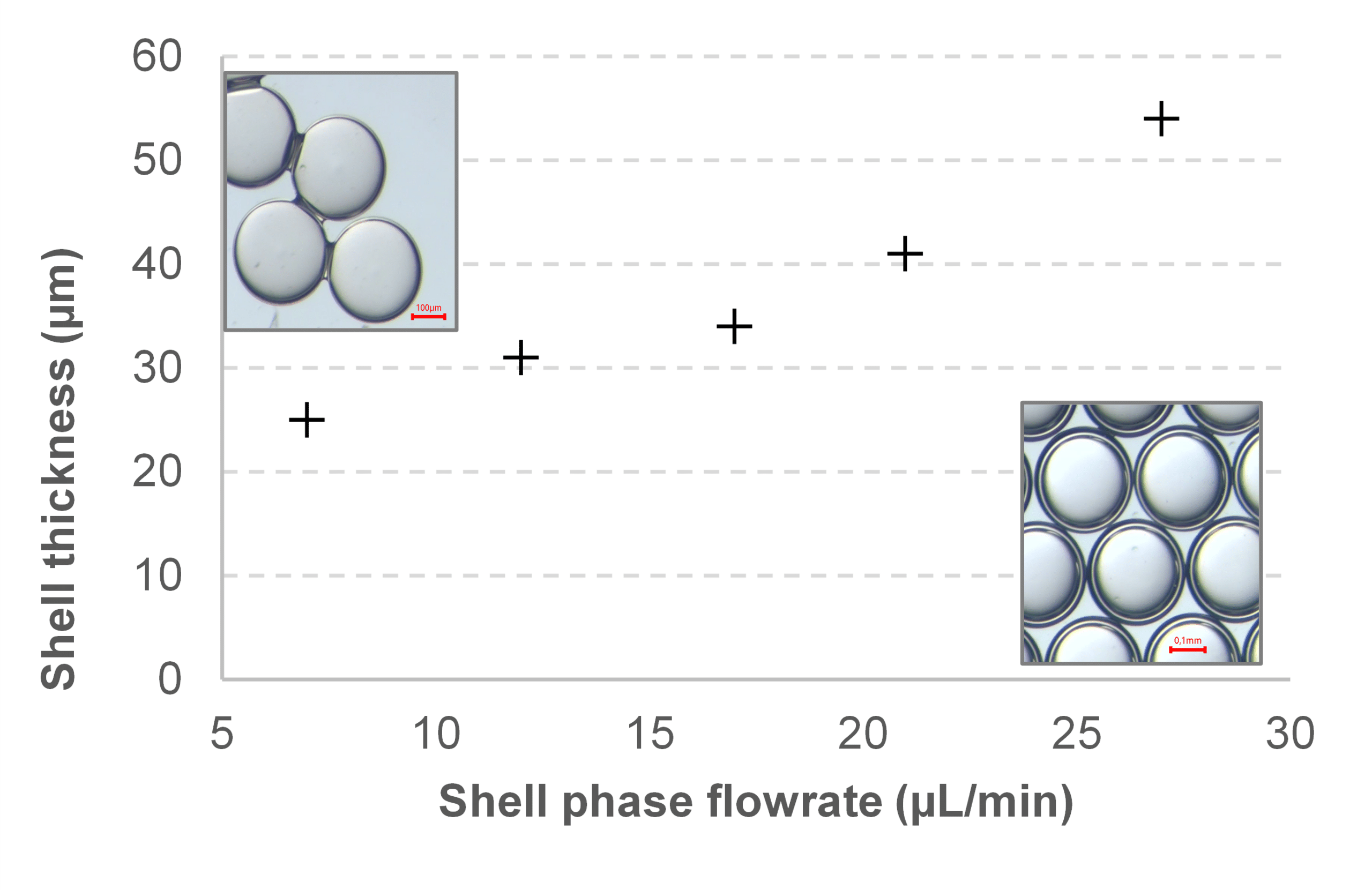
Shell thickness evolution in function of the shell phase flow rate. (M. Mettler et al., Chem. Commun., 2023, 59, 12739–12742)
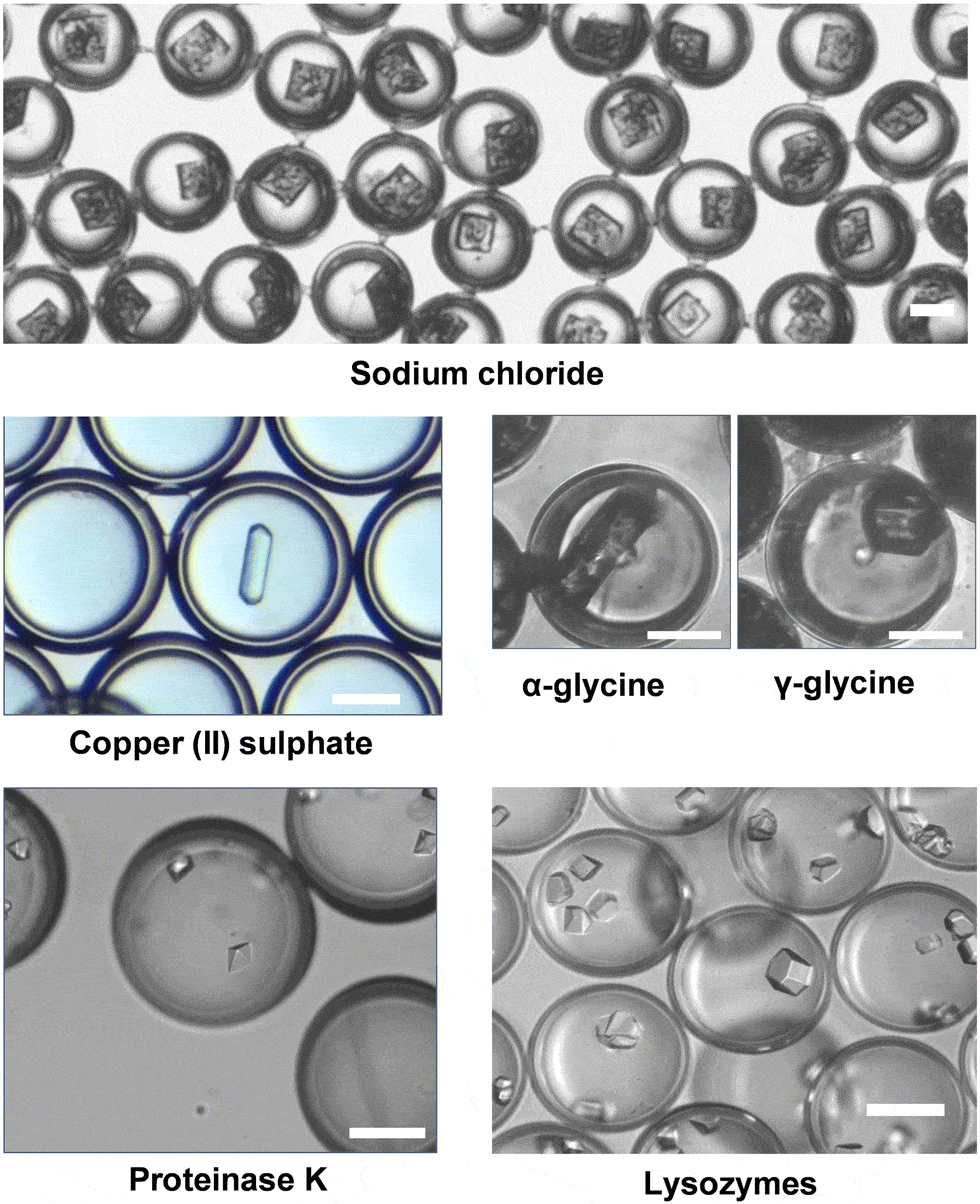
UV crosslinked microcapsules production (M. Mettler et al., Chem. Commun., 2023, 59, 12739–12742)
Related Application Note
Webinar Recording – Single crystal formation in core-shell microcapsules
You need more information? Don’t miss our exclusive webinar on “Controlled UV-crosslinked Microcapsule Production using Microfluidic Technology“.
Discover the latest advancements in core-shell microcapsule technology and its revolutionary impact on drug delivery, nutrient encapsulation, crystallization, and compound characterization.
Learn how to generate hundreds of identical UV-crosslinked microcapsules per second, produced by Secoya Technologies’ RayDrop and its all-in-one platform.
Specifications
Description | Product | Part Number |
---|---|---|
UV-crosslinked microcapsule production platform | – O-DE-STDWR-PTF – O-SP-UVL365-PTF | |
Double Emulsion Production Device | RayDrop double Emulsion 90-160-450 | O-DE-RDRPC02-EUP |
Fluid Handling System | – Link Module – Flow EZ 7 bar for all 3 phases | – LU-LNK-0002 – LU-FEZ-7000PCK |
Reservoirs | – Continuous phase: 50 mL Pcap with 50 mL Falcon tube Tubing: 500 µm – Shell phase: 15 mL Pcap with 15 mL Falcon tube Tubing: 125 µm – Core phase: 15 mL Pcap with 15 mL Falcon tube Tubing: 125 µm | – P-CAP50-HP-PCK – P-CAP15-HP-PCK – P-CAP15-HP-PCK |
Flow Meters | – Continuous phase: Flow Unit L – Shell phase: Flow Unit M – Core phase: Flow Unit M | – FLU-L-D – FLU-M-D – FLU-M-D |
Optical System | – Light source – Microscope objective (x10) – Specific color camera (up to 400 fps, 1µs integration time) – XYZ translation stages | N/A |
UV module | – UV led head 365: Wavelength: 365 nm Peak Irradiance: 1000 mW/cm2 at 10mm (with focus lens) Optics for 5 mm spot at 5 mm External Diameter: 12 mm – UV control Unit: Input voltage 84 – 264V AC Max power delivered: 50W (24 VDC – 2,1 A) – RayDrop holder, UV protective box and a glass capillary | O-SP-UVL365-PTF |
Tubing & Fittings | – Tubing: OD: 1/16 and 1/32 OD ID: 250 µm & 500 µm Materials: PFA – Manual valves: 4 way valves 2 way valves – Filters: 2 µm filter for continuous phase 2 µm filter for dispersed phase | N/A |
Wetted materials | – Platform: PEEK, PFA, PCTFE, PTFE, SS316L, GLASS – Sealing: FFKM | N/A |
Unit dimensions | – 61 x 46 x 43cm 3 (L x W x H) | N/A |
Weight | – 5 kg without the protective hood – 22 kg with the protective hood | N/A |
Droplet Size Range (Formulation and RayDrop configuration dependent) | –180 -400 µm | N/A |
OxyGEN
Control in real-time, protocol automation, data record and export |
ver. 2.2.0.0 or more recent |
Software Development Kit
Custom software application |
ver. 22.2.0.0 or more recent |
Related products
Microfluidic Double Emulsion Device
RayDrop Double Emulsion
See the offerMicrofluidic Complex Emulsion Production Platform
Platform for emulsions & droplets
See the offerEncapsulation Platform for FACS
Platform for cell encapsulation in DE droplets
See the offerMicrofluidic flow controller
Flow EZ™
See the offerBidirectional Microfluidic Flow Sensor
FLOW UNIT | FLOW UNIT +
See the offerBubble Trap
Remove air bubbles from your system
See the offerFluid Degassing Device for Microfluidic System
Microfluidic Fluid Degassing Device
See the offer
Expertise & Resources
-
Microfluidic Application Notes Creating Microcapsules With PEGDA Hydrogel Read more
-
Fluigent products manual User Manual – UV Module Download
-
Fluigent products manual Protocol – UV crosslinked microcapsule production platform Download
-
Fluigent Products Datasheets Datasheet – UV crosslinked microcapsule production platform Download
-
Microfluidics case studies Complex Emulsions as Real-Time Flow Sensor Read more
-
Microfluidics White Papers Double emulsion for the generation of microcapsules – a Review Read more
-
Microfluidic Application Notes Agarose Microcapsules Synthesis Read more
-
Microfluidic Application Notes PLGA microcapsules synthesis Read more
-
Microfluidics White Papers Droplet-based Microfluidics Read more
-
Microfluidic Application Notes UV-Crosslinking of Microcapsules Read more
-
Microfluidic Application Notes UV-Crosslinking of Microparticles Read more