Fluid Degassing Device for Microfluidic System
E-DEGAS-PCKDegasser
The fluid degassing chamber is an innovative solution for preventing the formation of air bubbles in microfluidic experiments. This chamber, featuring non-porous semi-permeable membrane, is perfect for aqueous-based microfluidic setups and a wide range of chemical substances. Paired with a vacuum or negative pressure source, the Degasser ensures maximum degassing capacity with minimal internal volume, enhancing precision and reliability in microfluidic instruments.
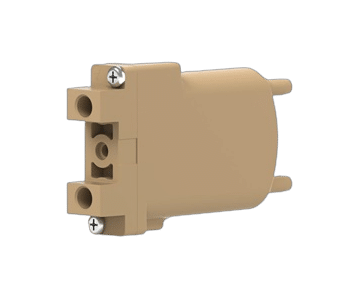
Features of the Degassing System
High Degassing Efficiency
The Degasser is highly efficient at removing air bubbles and dissolved gases from the liquid, connected to a vacuum or negative pressure source, it creates a pressure gradient across the non-porous semi-permeable tubing, which allows gas molecules to diffuse out of the liquid and into the vacuum chamber.
Compact
The Degasser is small and can be easily integrated into microfluidic setups. The device can be mounted on a standard microfluidic setup, saving lab space.
Small Internal Volume
The device has a low internal degassing membrane volume, which results in easier priming, lower flow restriction, reduced solvent changeover quantity requirements, and faster equilibration times.
Single Lumen Design
The single lumen design ensures a uniform and consistent flow of liquid through the chamber. This avoids the problems of variable flow rates and pressure drops that can occur in multi-lumen designs, where the liquid flows through multiple parallel channels.
Large Chemical Compatibility
The fluid degassing chamber has a high chemical compatibility with a wide range of solvents and substances used in microfluidic applications. The tubing is resistant to acids, bases, alcohols, ketones, esters, ethers, hydrocarbons, halogenated compounds, and many other organic and inorganic compounds. The tubing is also compatible with water-based solutions.
Easy to prime
The fluid degassing device is easy to prime and ready to use in minutes by applying a vacuum or negative pressure source to the vacuum port.
Inert Flow Path
The tubing is inert to most chemicals and does not adsorb or leach any substances into or out of the liquid. The tubing is also biocompatible and does not cause any adverse effects on biological samples such as cells, proteins, or DNA.
Why Degas Your Mobile Phase?
Gases dissolved in liquids can form bubbles when pressure or temperature changes, which can affect the accuracy, precision, and performance of the equipment. These air bubbles are undesirable in microfluidics, as even the smallest of them can compromise a biological or chemical experiment. They can damage cell membranes, disrupt droplet generation, block channels, or sweep biological and chemical agents away. Therefore, it is essential to prevent these bubbles, before they form and cause any damage. Adding a degassing device to your microfluidic setup may be necessary to avoid repeating an experiment due to bubble-related damage.
The Degasser is a device that efficiently removes these dissolved gases from the fluid stream, preventing bubble formation. The device is also able to remove already formed bubbles. This process reduces noise, improves baseline stability, reduces startup times and ensures more consistent results. It is particularly important in laboratory analysis equipment such as liquid chromatography, HPLC (High Performance Liquid Chromatography), ion chromatography and mass spectrometry. Machines for semi-conductor manufacturing or assembly, and instruments for immunology, hematology and in vitro diagnostics also typically deliver more consistent results with a degassing system included in the fluid path.
The Fluid Degassing Device Principle
Inside the degassing device the fluid flows through a short length of semi permeable tubing located in a small chamber. A partial void is maintained in this chamber by constantly running the vacuum at low speed. The dissolved gases migrate across the tubing wall under a concentration gradient produced by the vacuum as the solvent flows within the tubing. The gases that are removed are expelled, and the chamber is maintained at a constant, preset vacuum level. Depending on your system and needs in degassing efficiency,you can adjust the degassing process by varying the vacuum pump speed as needed.
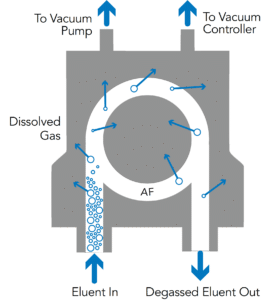
How to use the Degasser
Incorporating a fluid degasser into your microfluidic setup involves several steps:
1. Position the Degasser
The device should be positioned in this fluid path before any critical components of your experiment, such as microfluidic chips. This is to ensure that any dissolved gases are removed from the fluid before it reaches these components.
2. Connect it
Connect the inlet and outlet of the fluid degasser to your microfluidic setup A 1/16 OD tubing and standard 1/4″-28 fittings can be used for this purpose, and the flow rate through the degassing device can reach up to 10mL/min, but we recommend under 2 mL/min for optimal efficiency. Ensure that the connections are secure and leak-free.
3. Test the system
Once the microfluidic degassing chamber is connected, you should test your system to ensure that it is working correctly. This can be done by running a fluid through the system and checking for any bubbles or inconsistencies in flow.
4. Monitor and maintain
Regularly monitor your system to ensure that the Degasser is necessary. To extend the trap’s lifespan, flush the device with de-ionized or distilled water after use to prevent salt crystal formation.
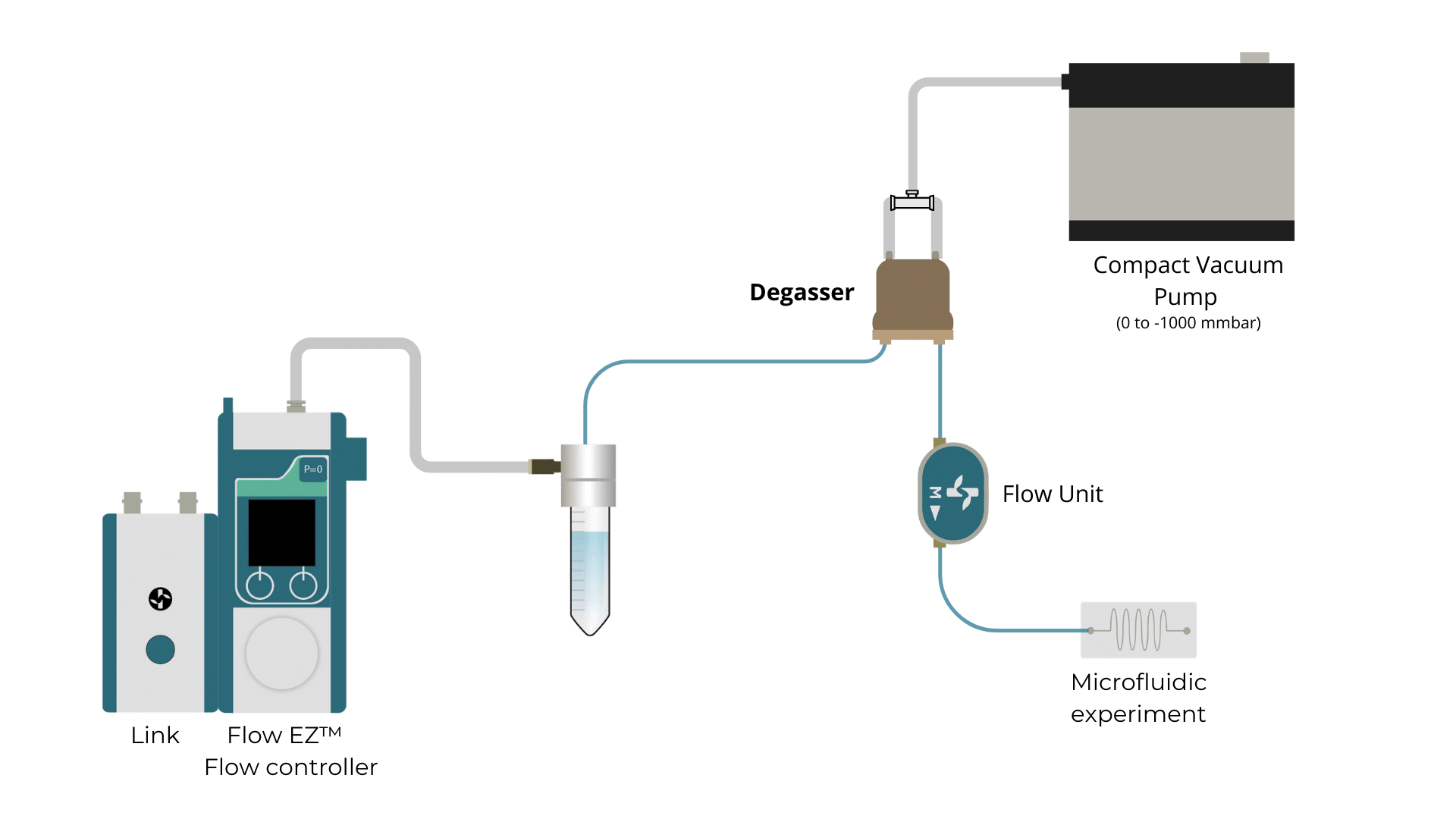
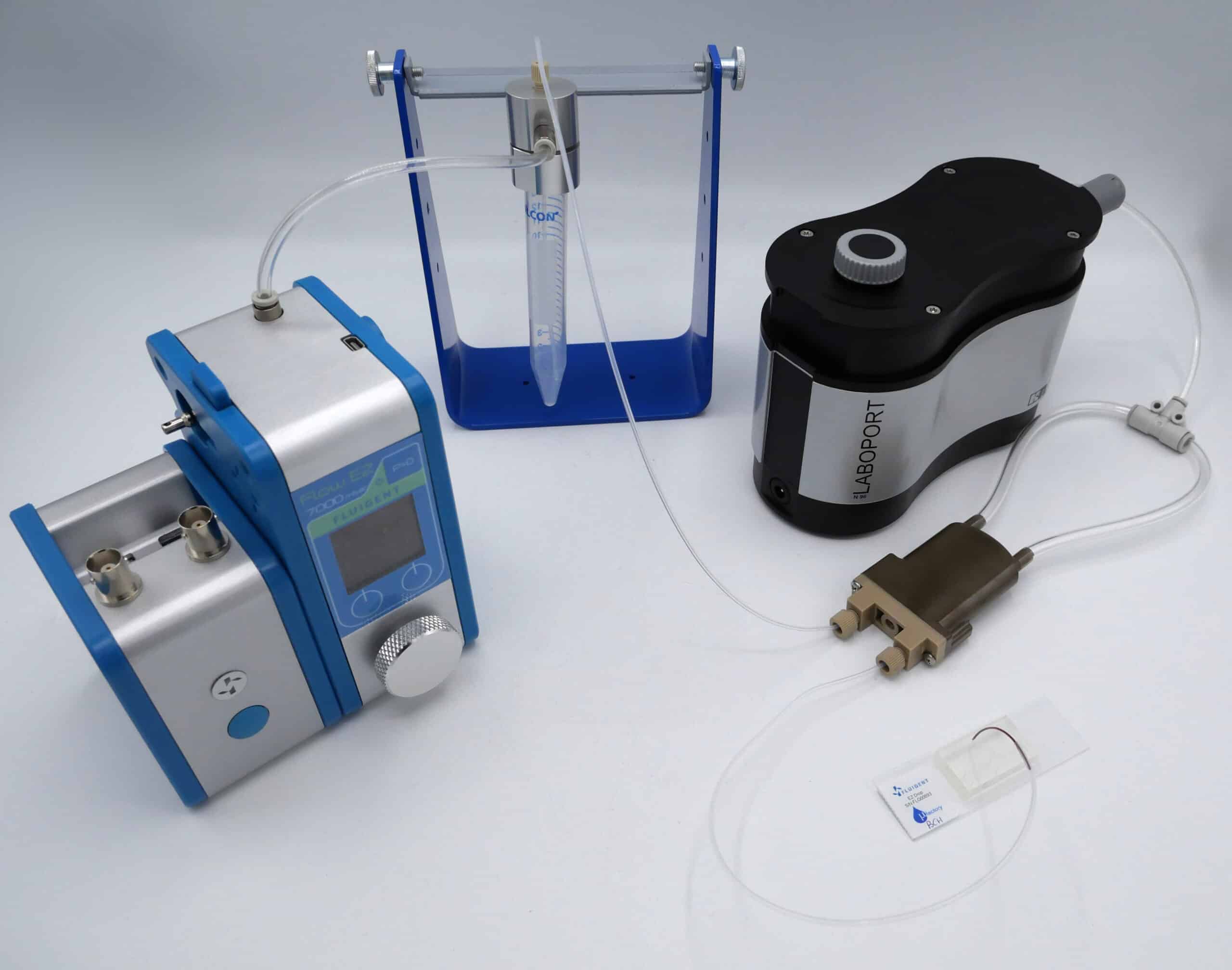
Technical specifications
Length (in) | 0.5 |
Tubing ID (mm) | 1.143 |
Liquid Connections | ¼-28 UNF, ¼-28 UNF |
Vacuum connections | Connections for 6mm OD pneumatic tubing |
Chemical Compatibility | Compatible With Organic Solvents and aqueous based systems. (See Solvent on Datasheet Compatibility Chart) |
Height (in) | 1.75 |
Internal Volume Per Channel (µL) | 480 |
Max Flow Rate (mL/min) | 10 |
Tubing ID (in) | 0.045 |
Recommended Flow Rate (mL/min) | 0 to 2.0 |
Degassing Channel Tubing | Teflon-AFTM |
Degassing Channel Pressure Rating | 70 PSIG (testing pressure) |
Vacuum Housing Material | PPS |
Width (in) | 2.48 |
Maximum pressure | Up to 7 bars |
Related products
Microfluidic flow controller
Flow EZ™
See the offerBubble Trap
Remove air bubbles from your system
See the offerBidirectional Microfluidic Flow Sensor
FLOW UNIT | FLOW UNIT +
See the offerCompact Vacuum Pump
VACUUM SOURCE
See the offerAirtight metal tube caps for microfluidics
P-CAP series
See the offer
Expertise & Resources
-
Fluigent products manual Degasser User Manual Download
-
Fluigent Products Datasheets Degasser Datasheet Download
-
Expertise Addressing Air Bubble Issues in Microfluidic Systems Read more
-
Microfluidics White Papers Droplet-based Microfluidics Read more
-
Microfluidics White Papers An exploration of Microfluidic technology and fluid handling Read more