A Microfluidic Pressure Controller Comparison for Your Ultimate Fluid Control System
In this comprehensive fluid control system comparison article, we rigorously test and discuss the differences between 3 categories of pressure controllers:
- Cost-effective
- Mid-range
- Premium pressure controllers
We emphasize evaluating product performance and examining their seamless integration into microfluidic systems, considering factors such as user-friendliness and integration capabilities.
How to choose the right microfluidic flow control system
Cost-effective pressure controller | Medium pressure controller | Premium pressure controller (Fluigent) | |
Accuracy | Medium | Good | Excellent |
Stability | Poor to medium | Medium | Excellent |
Response time and depressurization | + | ++ | +++ |
Sensor calibration | Not available | Not available | Available |
PID/Algorithm performance | No (analog I/O only) | Good | Excellent |
Ready to use | No (DAQ) | No | Yes |
Flow sensor integration | Not available | Not available | Available |
Flow rate regulation | No | No | Yes, through the Fluigent algorithm |
Microfluidic valve integration and automation | No | No | Yes |
Noise-free | No | Yes | Yes |
Price | Low | Medium | Medium to High |
Compatibility with microfluidics applications | Low | Medium | High |
Typical applications | Constant pressure supply: quake valves, semiconductors | Cell culture and basic droplet microfluidics | Droplet microfluidics, cell culture (OOAC), advanced fluorescence microscopy, microfluidic spectroscopy |
Table 1: Pressure controller comparison for microfluidic applications
Microfluidic technology is widely used in academic research for a myriad of applications in life sciences, chemistry, and food. It is also becoming increasingly popular in analytical device and bioreactor industries, as it brings a new level of analysis and offers several benefits, including more reliable results while minimizing reagent consumption.
Popular scaled applications today include microfluidics for cell biology, fine perfusion, and organ on a chip studies, or droplet microfluidics for biological encapsulation (digital PCR, organoids).
Advantages of Fluid Control for Industries
In the world of microfluidics, flow control is essential for reliable results. Several technologies are available on the market, including syringe pumps, peristaltic pumps, and pressure controllers.
Pressure control is a technology of choice in microfluidics as it usually offers higher performance and reliability compared to syringe pumps. Yet all pressure controllers available on the market are not equal, with some of them not adapted to microfluidics.
Each type has its own set of features and capabilities, catering to different budget constraints and research requirements. Depending on the user requirements, one will prioritize higher performance and reliability, which often comes with higher costs, while the other will optimize price at the cost of reduced performance.
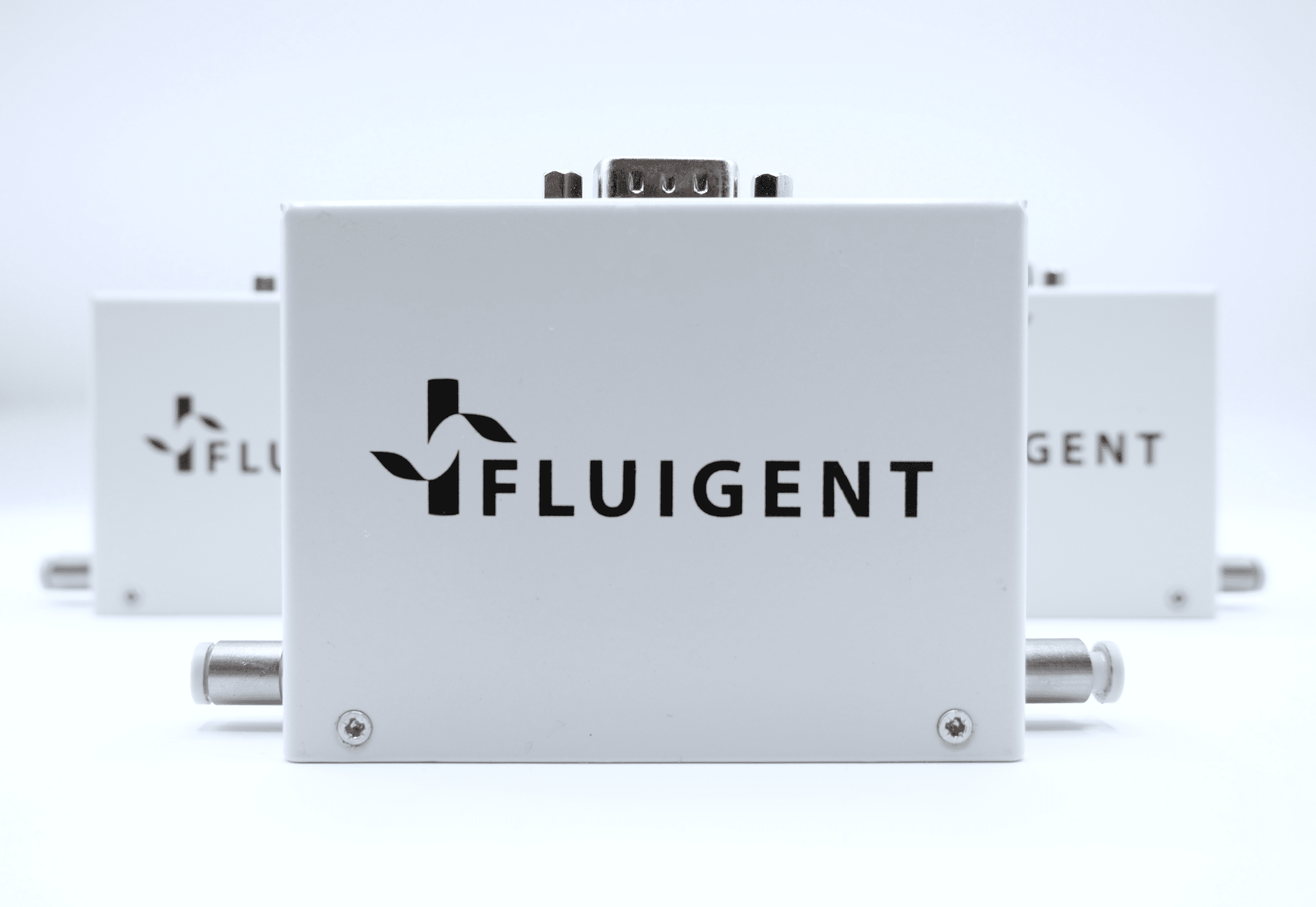
In the crowded jungle of pressure controllers and regulators, what is the best pressure controller for microfluidics?
What are the different pressure controllers?
We identified 3 different types of pressure controllers available in the market for users to choose from. We compared them in terms of cost-effectiveness and quality.
- Cost-effective pressure controllers are the most basic and affordable option. They typically have lower performance compared to the medium and premium options.
- Medium pressure controllers offer a balance between affordability and performance. They provide improved performance compared to cost-effective pressure controllers, but still find
- Premium pressure controllers, as the name suggests, offer the highest level of accuracy and stability. They are designed for applications where precision and reliability are of utmost importance, which is usually the case in microfluidics. Here the pressure controllers used are the Fluigent Flow EZ and F-OEM
Firstly, we compare the 3 pressure controllers in terms of performance (accuracy, stability, response time), and next focus on usability and integration capabilities. We finally discussed the achievable applications for each device.
Choosing a pressure controller based on performance
When choosing a pressure controller, a common practice is comparing specifications listed on product technical documentation such as product datasheet or user manual. There are several important parameters to consider such as product accuracy, repeatability, or response time.
Although a good approach to eliminate products that are beyond doubt out of specifications, it is a complex exercise as some manufacturers give specifications based on the sensor or valve that compose the pressure controller, while others tend to provide data based on real tests.
In addition to specifications, what makes the general performance of a pressure controller is its regulation algorithm. In fact, basic pressure controllers only provide analog communication based on voltage, while some can provide PID controllers that allow giving live feedback loops and adjusting the pressure based on the pressure sensor feedback. It ultimately affects pressure stability, accuracy, response time, and pressure transitions.
We here do a microfluidic pressure controller comparison based on accuracy, response time, and pressure transitions for cost-effective, medium-range, and premium pressure controllers with a pressure range of 0-1 bar.
How accurate and stable is your pressure controller
Accuracy is a crucial factor to consider when choosing a pressure controller. A pressure controller with high accuracy ensures that the desired pressure setpoint is achieved. In addition, pressure stability is a crucial factor to consider when choosing a pressure controller, as many applications rely on stable pressurization processes.
We perform accuracy and stability analysis by ordering a pressure of 750 mbar, measuring with an external calibrated pressure sensor, and keeping the ordered pressure of 750 mbar for more than 10 hours.
This approach allows us to identify how the devices behave under continuous operating conditions and to detect any drift or stability issues that only become apparent during prolonged operations.
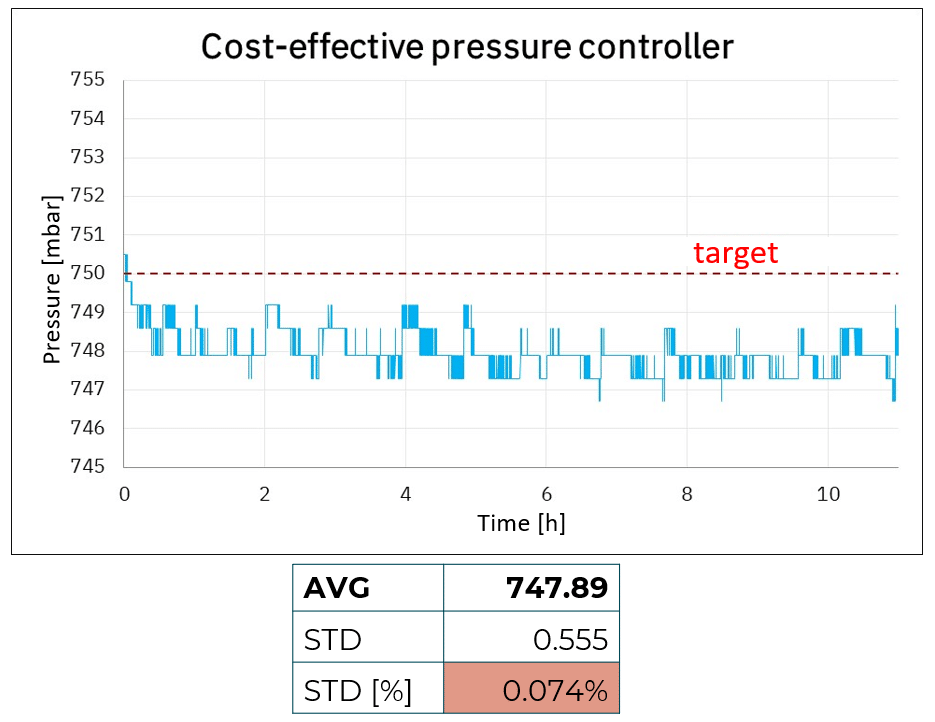
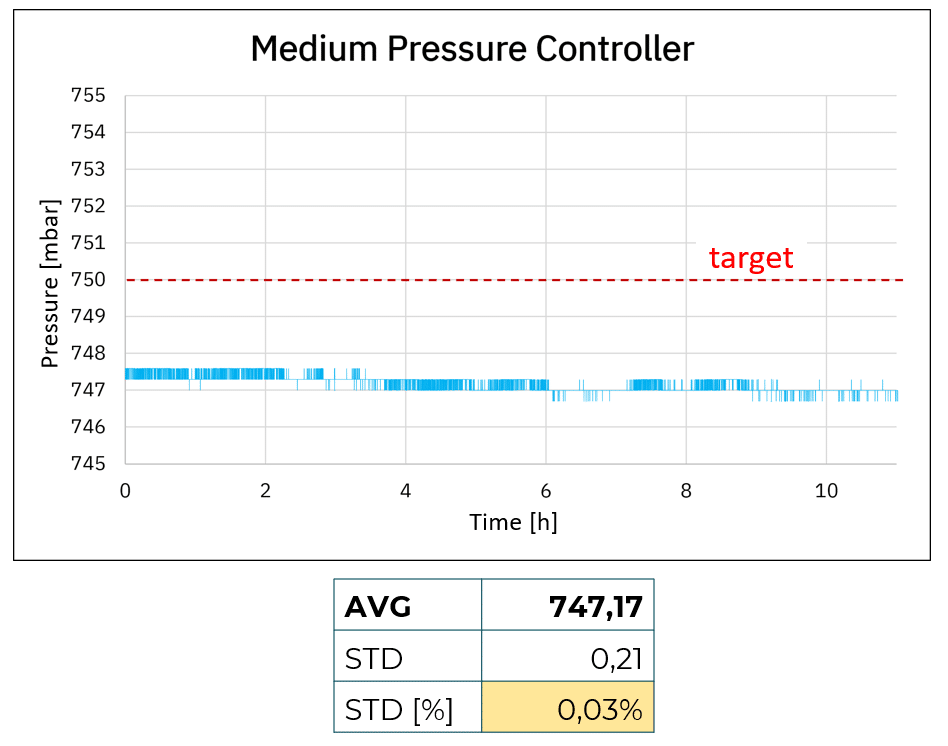
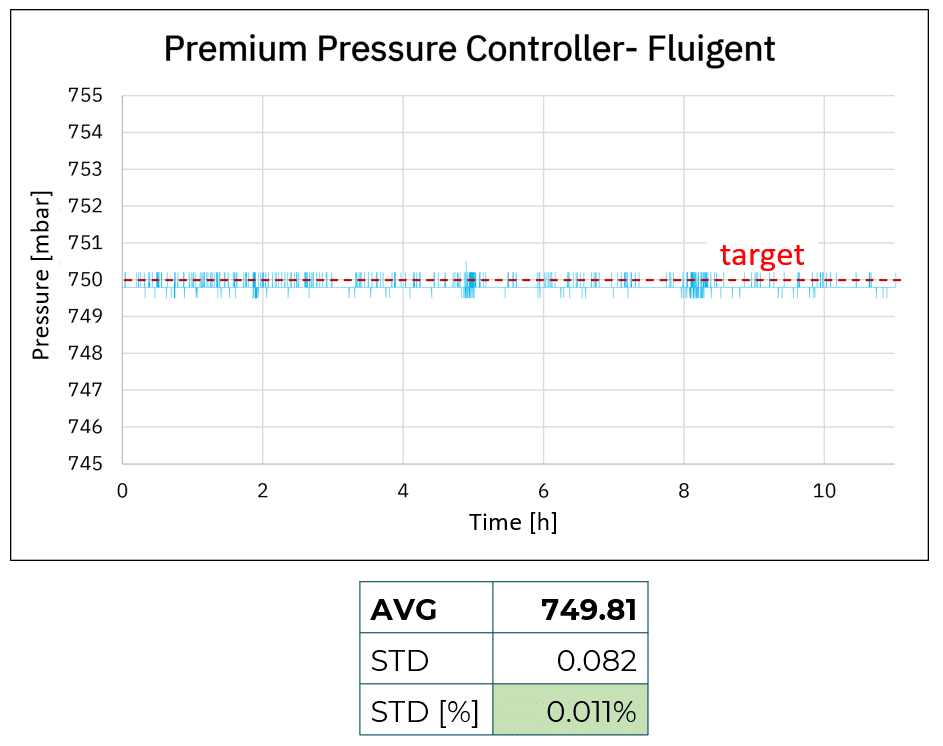
Figure 1: Accuracy and stability comparison using cost-effective, medium, and premium pressure controllers
Figure 1 shows pressure accuracy and stability for the cost-effective, medium, and premium pressure controllers. Looking at the average, it is possible to see that both cost-effective and medium-pressure controllers show a shift in accuracy compared to the targeted value of 750 mbar with a difference of more than 2 mbar. This is likely linked to the fact that both products do not have live calibration capabilities, inducing a shift compared to the targeted value, ultimately generating noise (see figure 2).
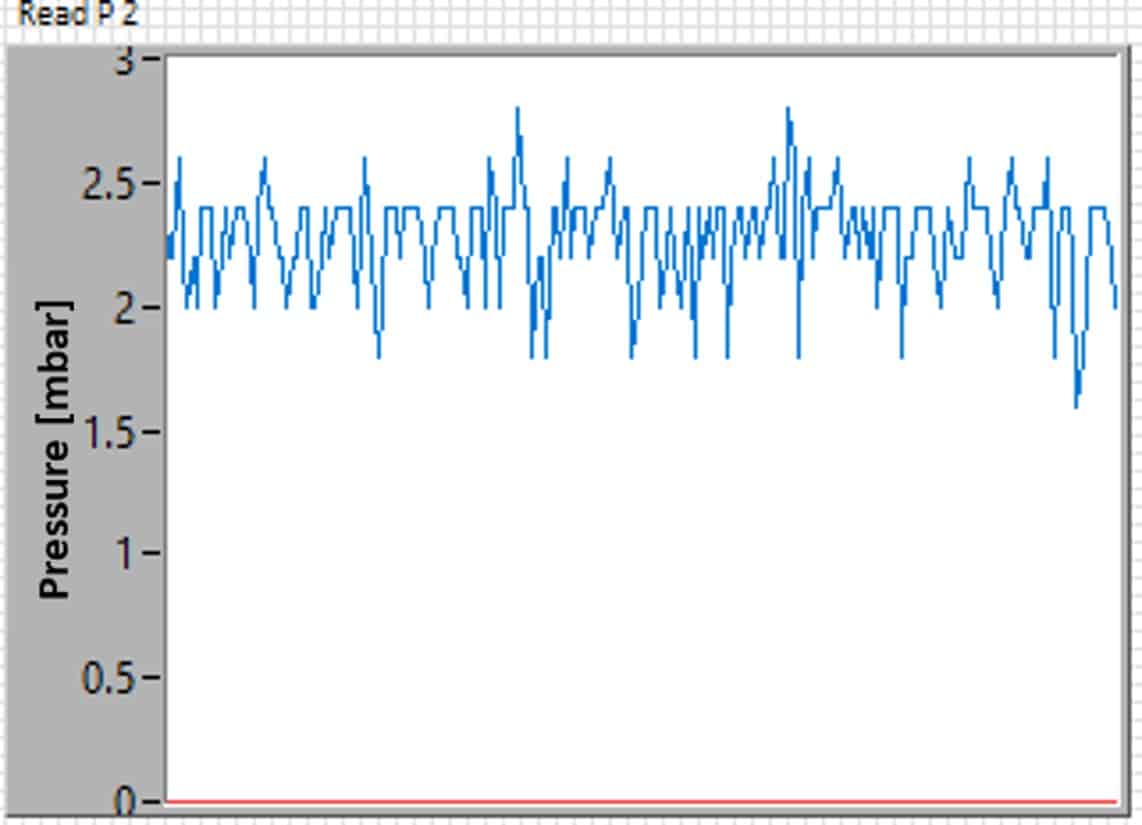
Enhanced stability and accuracy over the long term with the premium system
Using the premium pressure controller, the average value is 749.81 mbar, +/- 0.082 mbar. The premium pressure controller is the most accurate device with less than 0.2 mbar shift compared to the targeted value, making it the most performant product in terms of accuracy.
Another parameter we can analyze here is stability. We observe that with the cost-effective system, 750 mbar is achieved at the start of the experiment but in less than an hour we can observe a shift in the applied pressure, transitioning from 749 mbar after ~30 min and 748 mbar after a few hours. We observe similar pressure drift with the medium pressure controller, with a lower degree of magnitude (747.5 to 747 mbar).
Utilizing the premium pressure controller, the pressure of approximately 749.8 mbar remains stable for over 8 hours without exhibiting any drifts. Additionally, we observe enhanced stability and accuracy over the long term, as it is consistently maintained within the required pressure range with commendable stability.
Response time: how fast do you want to change pressure?
Response time is another important factor to consider when choosing a pressure controller. A pressure controller with good performance will be able to quickly respond to changes in pressure and maintain stability.
The response time of a pressure controller is a critical factor in microfluidics due to the precise and often delicate nature of processes within these systems. A pressure controller with a quick and accurate response time ensures that when setpoints or external conditions change, the system can adapt rapidly and maintain the desired pressure with minimal overshot or oscillations. This is essential for maintaining the integrity of experiments or processes, as delays or inaccuracies in pressure adjustment can result in compromised data, ineffective fluid control, and potentially damage sensitive microfluidic components.
We here perform 2 response time tests: pressure increase (400 mbar -> 500 mbar) and pressure decrease (500 mbar -> 400 mbar).
We define the response time as the time to reach 98% of the targeted value and remain in a tolerance of 2% of the targeted value. Note that we cannot perform this test on the cost-effective pressure controller as it is controlled through analog I/O only and does not include a PID.
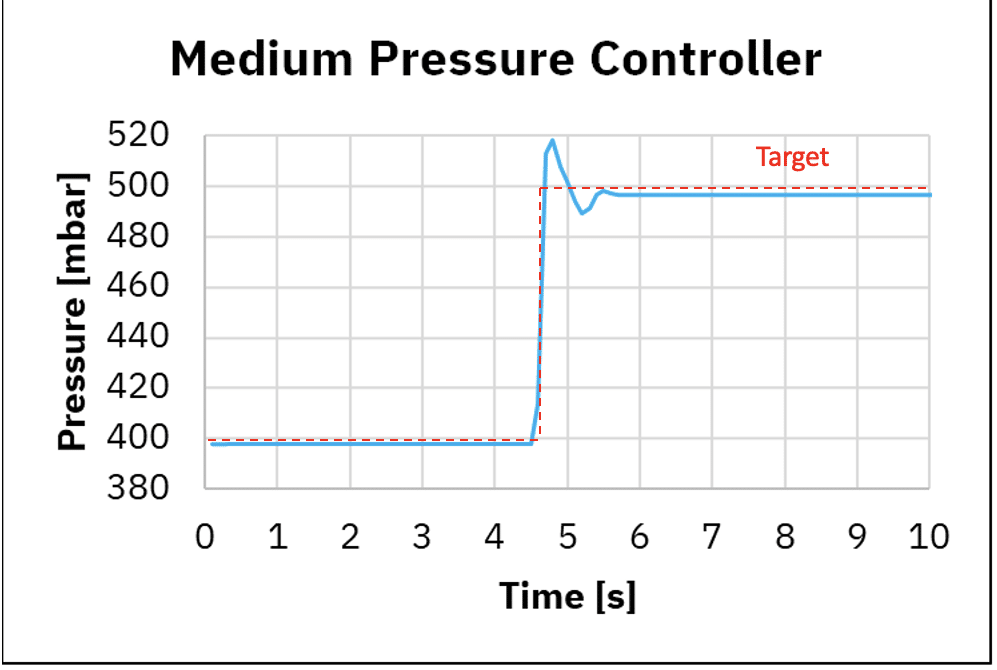
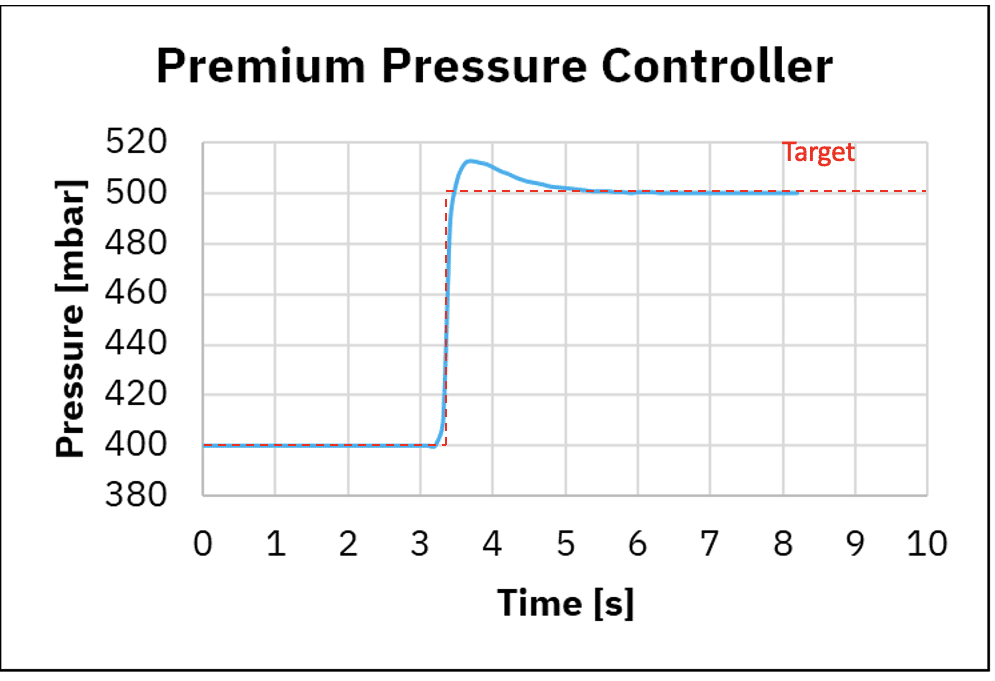
Figure 3: Response time using medium pressure controller and premium pressure controller
Response time 400 to 500 mbar | Response time 500 to 400 mbar | |
Medium Pressure Controller | 0.8 s | 0.7 s |
Premium Pressure Controller | 0.8 s | 0.1 s |
Table 2: Pressure controller comparison for microfluidic applications
A Better response time with the premium fluid controller
Figure 3 shows pressurization and depressurization using the medium pressure controller and premium controller. When using the medium pressure controller, for pressurization we observe the time to reach 98% of the targeted value is 0.8 seconds while using the premium pressure controller 0.8 seconds. For depressurization we observe the time to reach 98% of the targeted value is 0.7 seconds while using the premium pressure controller 0.1 seconds.
This shows the medium pressure controller and premium pressure controller have similar response time for pressurization for a transition at 100 mbar, while depressurization is about 10 times faster with the premium pressure controller.
In addition, with the medium pressure controller, we can observe minor pressure oscillations and overshoots after reaching a stable phase, which also originates from the regulation algorithm performance.
Additionally, when one needs to stop a fluidic protocol, depressurization time will depend on the pressure controller used. Graph 4. shows the depressurization time from 500 mbar to 400 mbar using the medium and premium pressure controllers. We can observe it takes 0.7 s and 0.1 s using the medium and premium pressure controllers respectively.
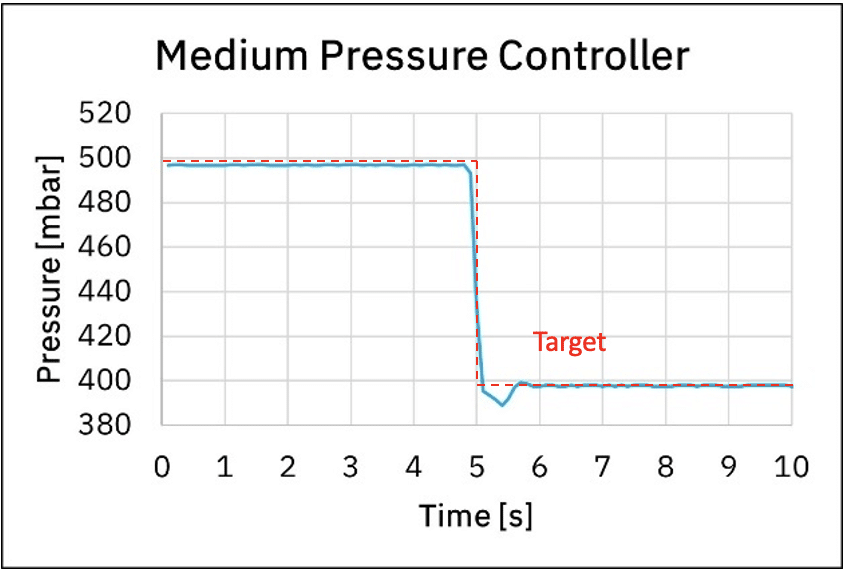
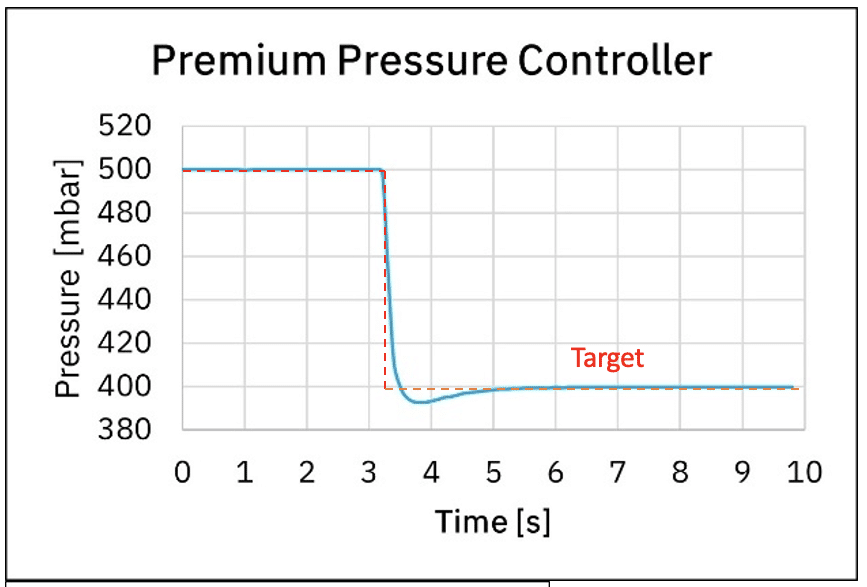
Figure 4: Response time using medium pressure controller and premium pressure controller
Depressurization time has a great impact on microfluidic protocols, as during the depressurization time liquids are still injected even though the experiment has ended. Precious liquids injected during the depressurization time are wasted, which ultimately has an impact on experiment costs. Depending on the system used and the related fluidic resistance, depressurization time can take more than tenths of seconds!
The smoother the better: Product algorithm and PID ultimately affect performance
As mentioned in the above paragraphs, product specifications do not make it all. PID and algorithms also have an impact on performance. Figure 5 shows the pressure curvature during a transition from a higher pressure for the medium pressure controller. We can observe some jabbering when transitioning to 100 mbar, which is not observed using the premium pressure controller (figure 5).
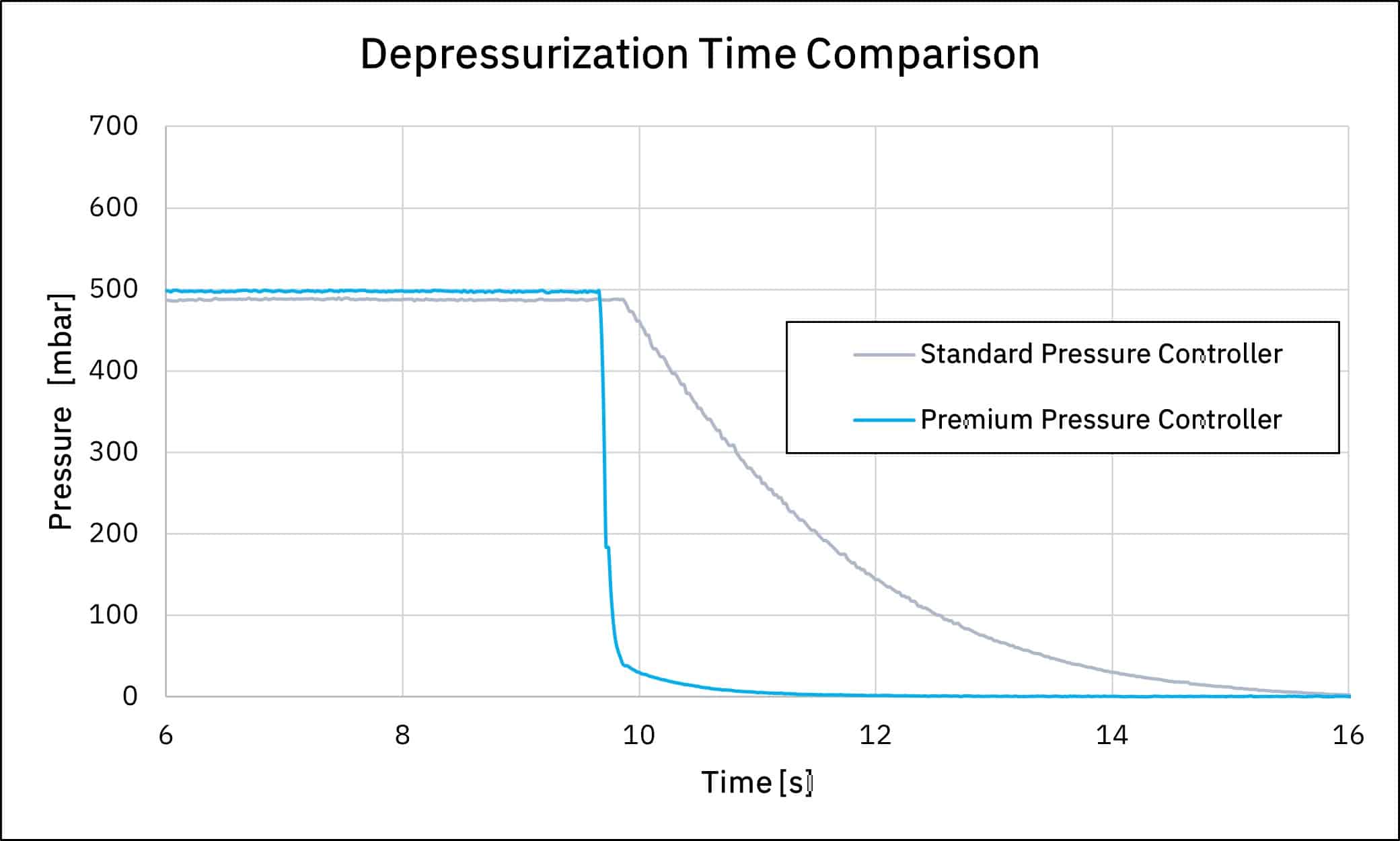
In our comparative analysis between pressure controllers, we observed noticeable differences in performance, particularly in terms of accuracy and stability. Both cost-effective pressure controllers exhibited more pronounced fluctuations and required a longer duration to achieve a state of equilibrium. Additionally, it stabilized within a less precise pressure range compared to its counterpart.
On the other hand, the premium product demonstrated a remarkably smoother and more stable transition profile. It efficiently and rapidly attained stability, aligning closely with the desired precision levels.
This superior performance in maintaining consistent pressure control under varying conditions underscores the premium product’s advanced engineering and design.
Such characteristics are particularly vital in microfluidics applications where exact pressure control is crucial for the integrity and accuracy of the results.
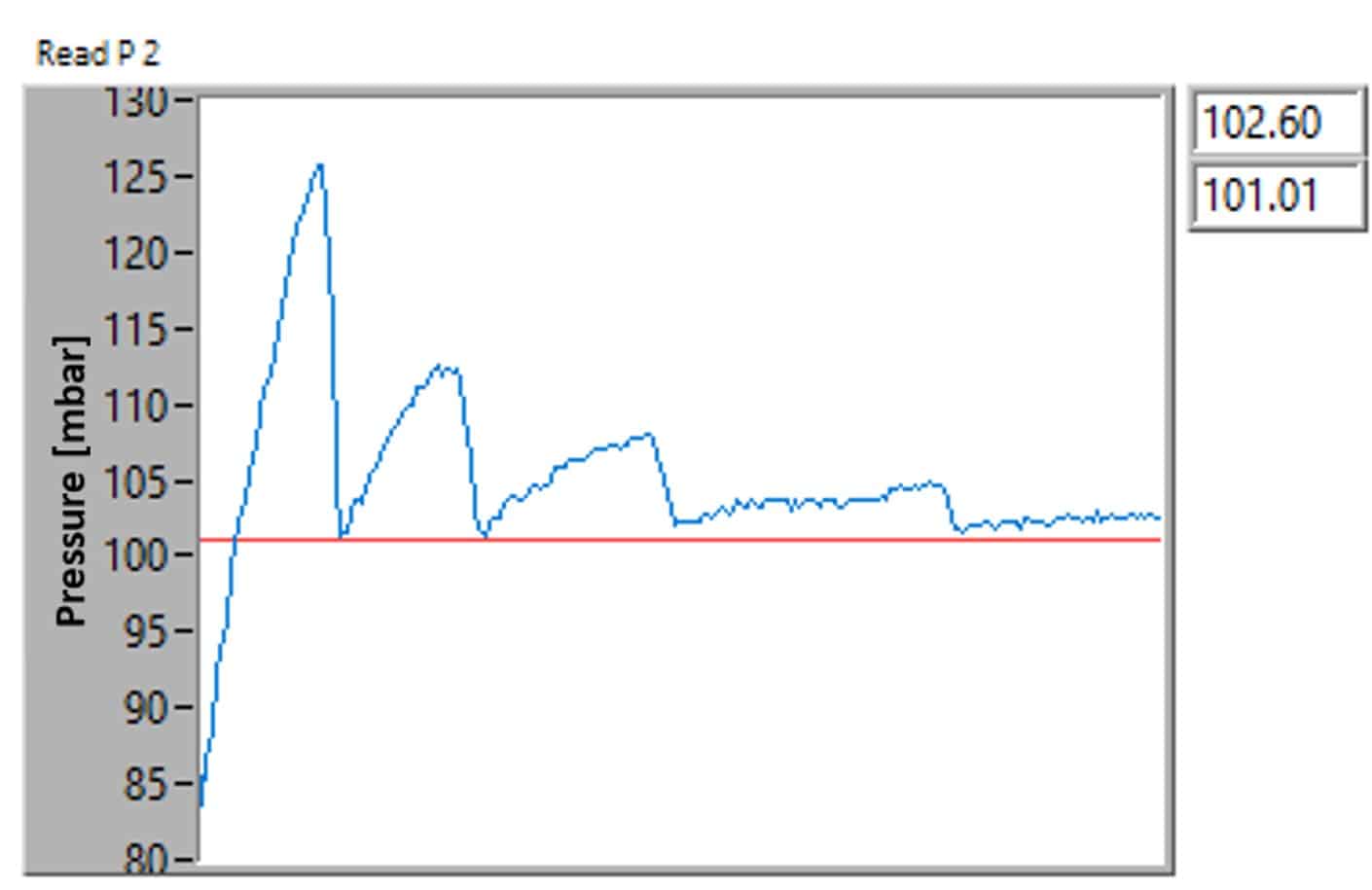
Microfluidics require expertise for integration
Time to market: Is your pressure controller ready to use and easy to integrate?
When using simple pressure controllers, they generally do not come with ready-to-use software and high-level functions. For the low-cost and medium-range models, an analog-to-digital communication converter was required to facilitate proper data acquisition and interpretation.
This additional step needs to be considered in terms of additional internal development and time to market. We present below a microfluidic pressure controller comparison based on ready-to-use capability:
- Cost-effective pressure controller: needs to develop an additional DAQ device for commanding the system. The absence of a need for an analog-to-digital converter indicates a more advanced and integrated design, aligning better with modern digital interfaces and standards.
- Medium range pressure controller: Although there is no need for an additional DAQ (all internal electronics integrated into the device), it is required to develop a custom software interface to start measurements.
- Premium pressure controller: Ready-to-use software with advanced dedicated SDK available in several languages (Python, C++, C#)
Mastering the microfluidic environment: pressure controllers for flow rate control, valve management, and automation
What is the difference between flow control and pressure control?
Many processes in microfluidics demand precise monitoring and regulation of flow rates, along with the integration of valves to automate complex workflows, ensuring repeatability and reliability.
Efficient flow rate monitoring facilitates precise volume injections, while valve automation proves essential for tasks such as sample preparation, multiplexing, or cleaning processes.
Explore our article for insights into the challenges of fluidic valve automation, and the advantages offered by our F-OEM flow control platform.
In contrast to traditional pressure controllers, achieving advanced regulation capabilities by integrating and controlling microfluidic flow sensors and valves demands expertise in electronics, mechanics, and microfluidics.
Synchronization among all microfluidic components is pivotal for seamless automation. With classical pressure controllers, integration should be done by the microfluidic expert resulting in a potentially costly, time-consuming, and resource-dependent process. This could impact time to market and compromise the final system’s reliability.
Our premium microfluidic pressure controller stands out by seamlessly interfacing with in-house microfluidic flow sensors and valves. Commanding these components requires no additional development, through dedicated software and SDK, offering a streamlined solution that enhances efficiency and reliability without sacrificing time to market.
- Cost-effective pressure controller: development needed
- Medium range pressure controller: development needed
- Premium pressure controller: Ready-to-use with Fluigent flow sensors and valves
What are the typical applications achievable with the above pressure controllers?
As seen above, each pressure controller has distinctive performance, ranging from poor/medium to excellent depending on the parameter. Microfluidic applications most generally require highly demanding fluidic performance. Consequently, all pressure controllers discussed here do not cover the complete list of microfluidic applications.
- Cost-effective pressure controller: The cost-effective pressure controller has average to poor performance in terms of accuracy, or stability. In addition, PID is not available. It makes the product limited to applications where pressure should not be highly stable, without any fast (a few seconds) pressure changes over time. It is suitable for low-precision analytical devices with flow rates higher than a hundred milliliters per minute. Typical applications include gas chromatography and semiconductor processes. In microfluidics, it can be used for injecting pressure for opening/closing valves, such as in quake valve processes.
- Medium range pressure controller: The medium pressure controller has average to great performance in terms of accuracy and stability. A basic PID is available which can be useful for less demanding microfluidic applications. It can be useful for microfluidic cell perfusion and culture, and in some cases of droplet microfluidics where production should remain stable and without frequent flow rate changes. It is however limited to complex microfluidic protocols, or where processes require minimal use of sample reagents.
- Premium pressure controller: The premium pressure controller from Fluigent was developed to meet all microfluidic application requirements. Consequently, general performance is excellent, including excellent accuracy, stability, and response time. Its patented regulation algorithm allows to finely adjust pressure during any microfluidic protocol, and flow sensor and valve integration is implemented by default, allowing complex microfluidic protocols to perform. Applications include amongst others droplet microfluidics for digital PCR and encapsulation applications, cell biology for organs on chip and cell culture, cell sorting and flow cytometry, and advanced fluorescence microscopy where all multiplexing protocols must be automated while saving previous sample reagents.
Related products
Expertise & resources
5 reasons to choose OEM pressure controllers over OEM syringe pumps for microfluidic applications
Read more- Expert Reviews: Basics of Microfluidics
Flow Control Technologies: Comparison between peristaltic, syringe and pressure pumps for microfluidic applications
Read more - Expert Reviews: Basics of Microfluidics
Choosing the Right Microfluidic Pressure Range
Read more Valve Automation with the F-OEM for Microfluidic Applications
Read more