Valve Automation with the F-OEM for Microfluidic Applications
Advantages of automating fluidic valves in industrial processes
Microfluidic valves help to control the flow of small volumes of fluid. This control allows microfluidic devices to become more complex, with a higher degree of automation depending on the need of the application. In analytical and diagnostic devices, for example, these valves control the flow of neutral and aggressive fluids, such as blood, chemicals, and buffers.
Starting fluid automation and valve management with the F-OEM
The video below illustrates the fast and automated sequential fluid injection of the different dyed solutions that can be implemented using the F-OEM. Figure 2 shows the measured flow rate and implemented pressure as a function of time.
All the switch events are also shown and correspond to the peaks on the fluidic line. During the switch events, the applied pressure is automatically regulated to keep a fluid flow rate of 500 µL/min during the whole protocol. Peaks are inherent to the valves switching due to their respective internal volumes.
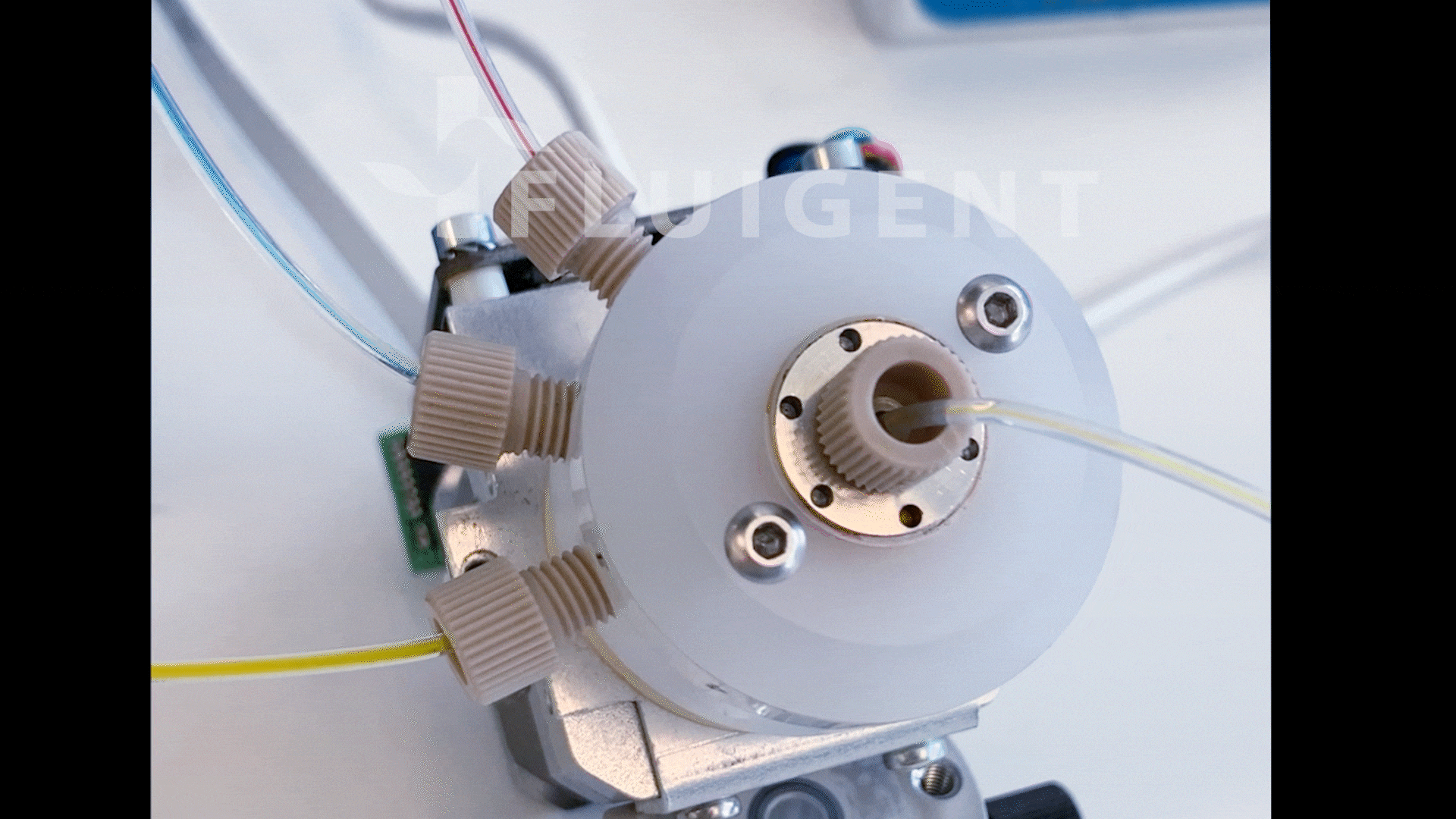
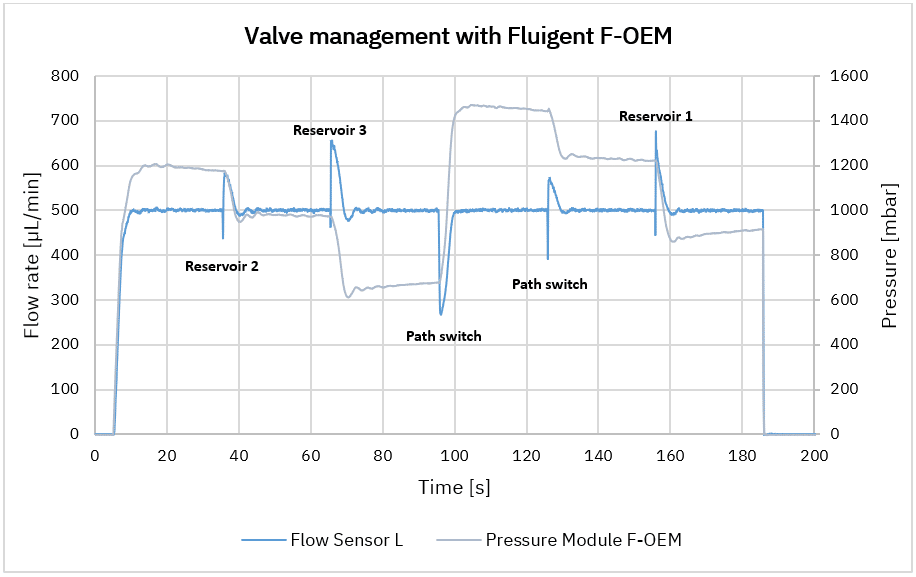
The targeted flow rate of 500 µL/min is kept constant during the whole protocol, with peaks < 5 s that are inherent to the fluidic system and correspond to the fluidic switches. At regions without peaks, the estimated flow rates average, standard deviation, and related accuracy are respectively 500,5 µL/min, +/- 1,5 µL/min, and 0.3%. Fast pressurization and depressurization are possible via Fluigent pressure controllers integrated into the F-OEM.
From sample preparation to cell sorting
- Electric rotary valves are used to sequentially inject liquids or dispatch liquids in several paths.
These valves can be used in high-precision fluorescence microscopy, where a large number of labels are processed. Another example is microfluidic-based analytical devices including spectroscopy, photometry, separation, and reactors. Those applications usually require precise sample preparation, and the ability to automatically switch from analytical samples to buffers while minimizing the amount of reagents used. - 2/2 or 3/2-way valves are used to perform fluid separation. They are useful in cell sorting applications where samples containing a detected cell or analyte of interest can be separated from the main flow path for further investigation. It is also widely used for cleaning and waste handling in analytical equipment.
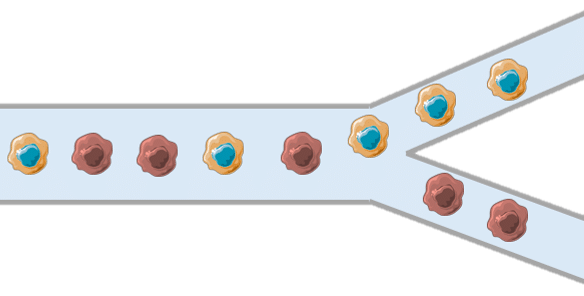

Figure 3: Examples of applications using fluidic valve automation. Cell sorting (up) and sample preparation (down).
How to efficiently integrate your microfluidic modules?
Component integration and time to market
Developing a fluidic system and integrating valve automation requires fluid handling components (pressure controllers, syringe pump, etc.), fluidic valves, and related electronics and software for communication and automation. To ensure the proper functioning of the fluidic system and the success of the application, seamless coordination between all the fluidic components is required. The automation and creation of the interface can be costly, time-consuming, and resource-dependent, which would ultimately impact time to market and affect the final system reliability.
The F-OEM: A turnkey solution for efficient prototyping and integration
Fluigent develops and provides turnkey fluid management systems, consisting of pressure sources, pressure-based flow controllers, and fluidic electronic valves dedicated to microfluidics. When using Fluigent systems, users will:
- Gain development time and reliability as ourvalves include the necessary electronics to communicate with other Fluigent components
- Experience fast prototyping and integration through Fluigent’s OxyGEN software and SDK
- Increase compactness as ourvalve module is integrated into the F-OEM pressure controller
The system used below consists of the following components:
- F-OEM with its subcomponents (integration board, OEM pressure controller, valve module)
- Fluigent M-X: Rotary multi-port OEM microfluidic valve
- Fluigent 2-X: 3-port/2-way bidirectional OEM microfluidic valve
- FS Series fluidic OEM flow sensor
Below is a typical fluid handling setup that can be used for applications such as sample preparation, multiplexing, pipetting, and sorting. One pressure controller is used to pressurize 3 reservoirs containing specific solutions, that will be injected in turn and sorted using the M-X and 2-X valves.
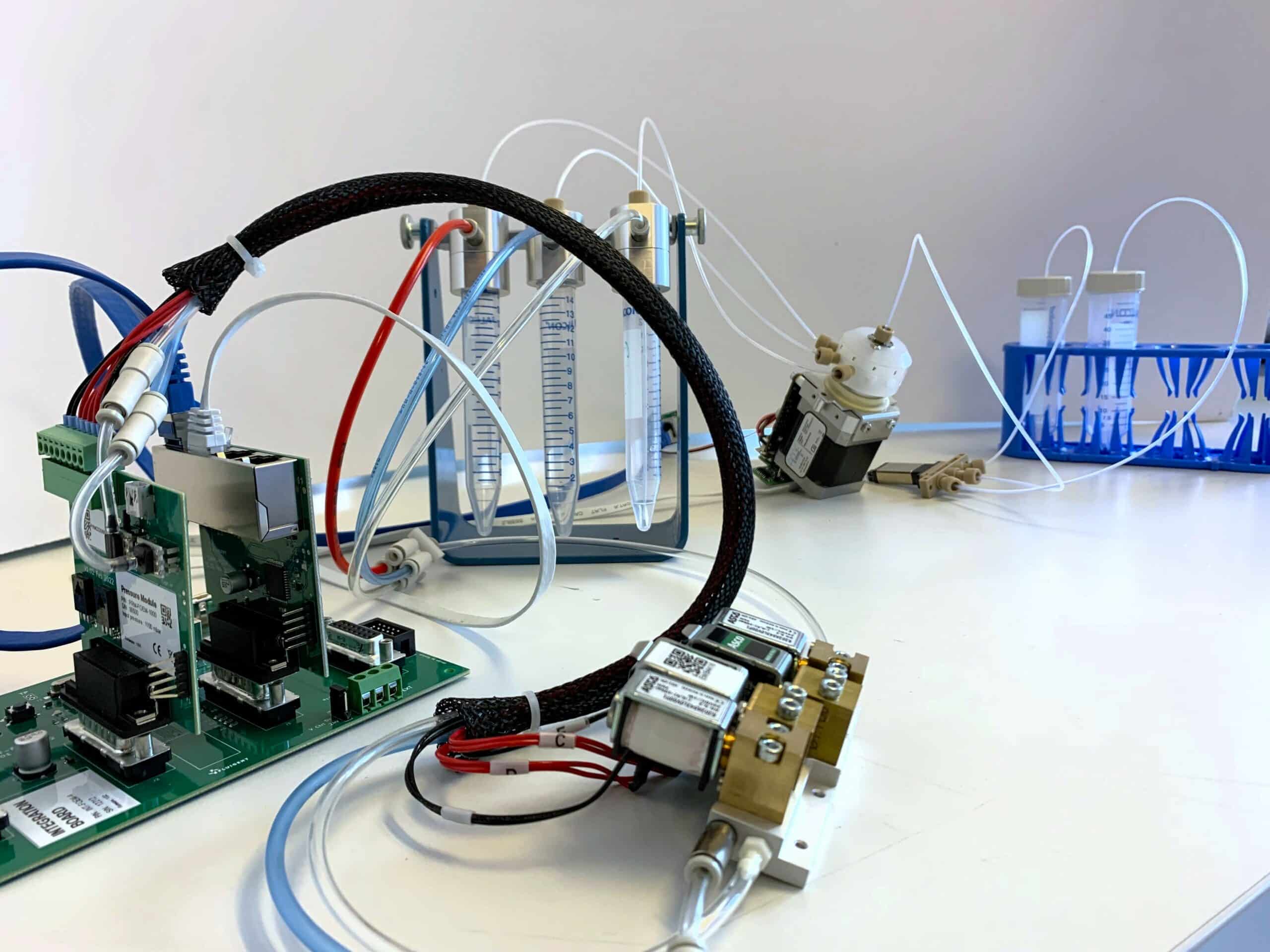
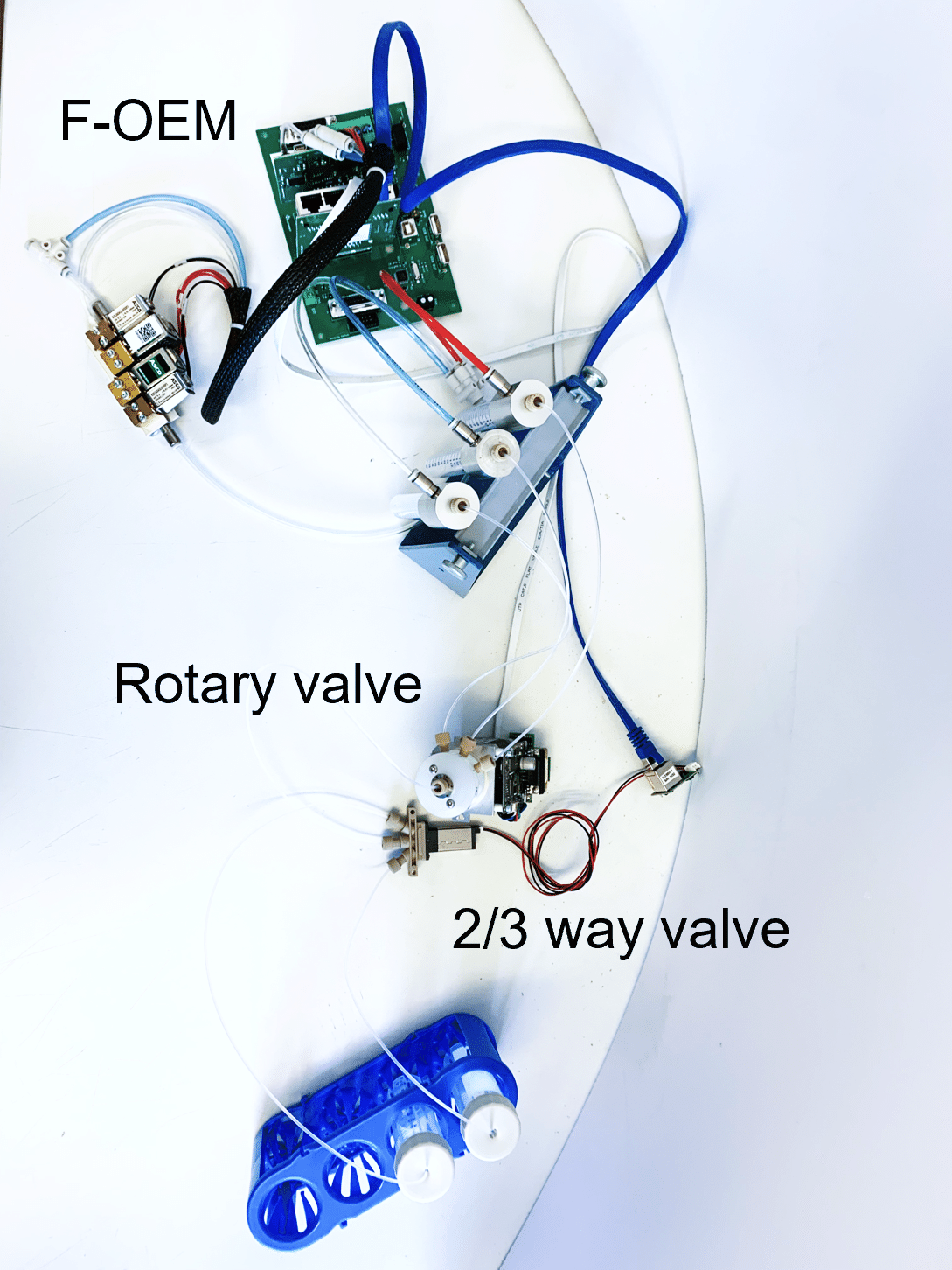
Figure 4: Fluigent’s microfluidic OEM system dedicated to fluidic valve automation consisting of the F-OEM pressure controller, and the 2-X and the M-X valves
Fluigent software for complete automation
Quick testing using OxyGEN software
For starting immediate tests with prototypes, Fluigent’s OxyGEN software is available for fluid management. All components can be driven using the “live control” tab, and more complex protocols can be computed on the “Protocol tab” for starting fluid automation (figure 5).
In typical valve automation, protocols such as in sample preparation, sorting, or cleaning several fluids are injected sequentially, while the main fluidic line can be switched to collect samples or manage waste.
We here simulate a typical sequential fluid injection protocol by injecting 3 dye solutions from 3 separate reservoirs.
Figure 5 shows the protocol implemented on OxyGEN. The implemented flow rate is 500 µL/min during the whole experiment. We performed the following sequence:
- Reset all pressures
- Flow rate at 500 µL/min
- Set 2-X at position 1 (ensures right positioning at protocol start)
- Set M-X at position 1, wait for 30 s
- Set M-X at position 2, wait for 30 s
- Set M-X at position 3, wait for 30 s
- Set 2-X at position 2
- Set 2-X at position 1
- Set M-X at position 1, wait for 30 s
- Set pressure at 0 mbar
The video shows the protocol running. Protocol can be monitored during the entire process. Real time information on the flow rate, pressure, and valves position is available on the live control tab of OxyGEN software.
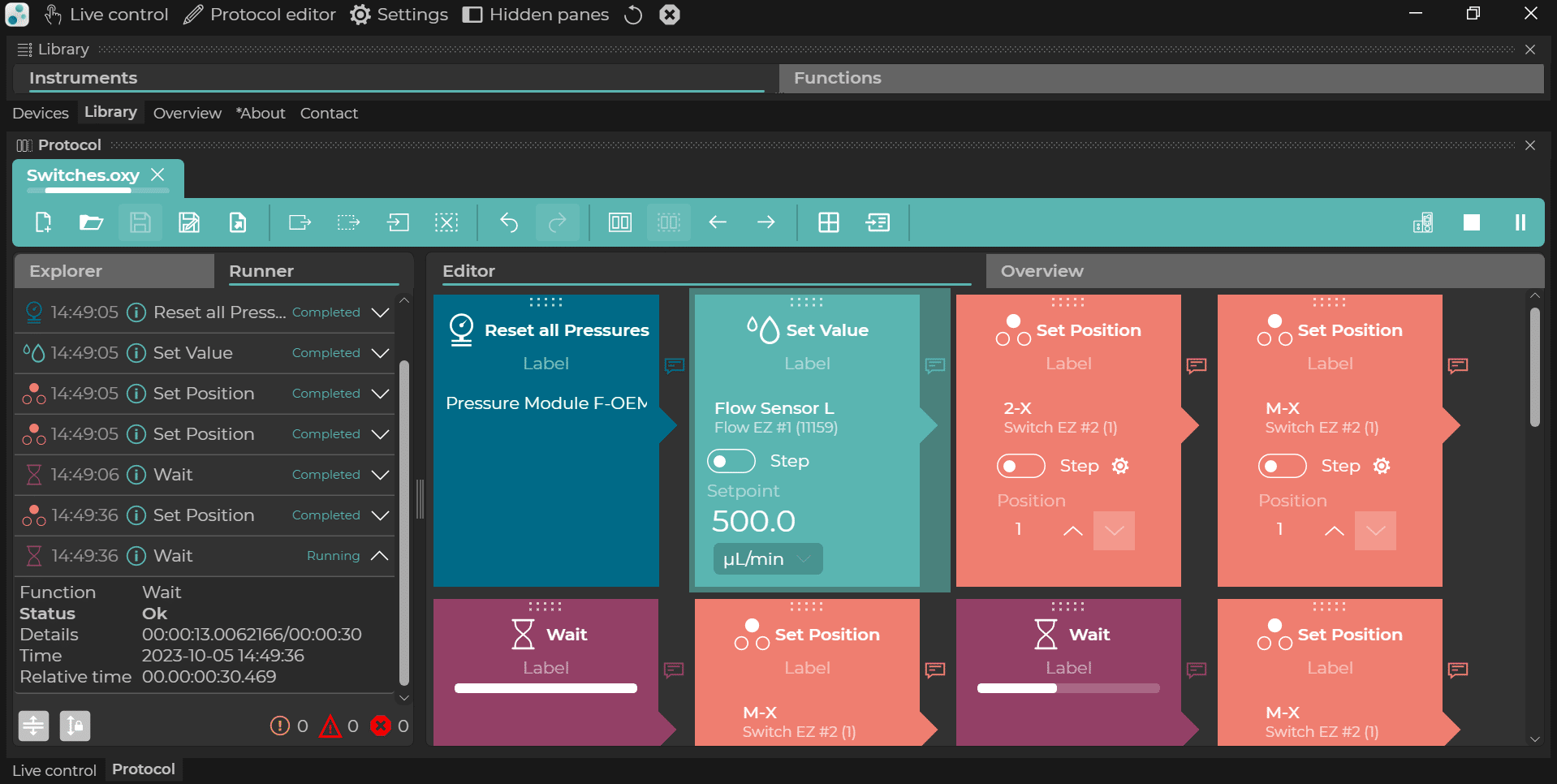
Seamless integration through Fluigent SDK
When a protocol is fully validated, users can use Fluigent SDK, which consolidates all functions available in OxyGEN. This gives external applications the ability to integrate Fluigent devices.
The SDKhas been designed in several languages, including LabVIEW, C++, C#.NET, Python, and MATLAB. Below is the Python equivalent of the protocol implemented above in our OxyGEN software.

Our fluidic modules can automate fluid tasks for milli and microfluidic applications
The results above demonstrate the capabilities of the F-OEM coupled to Fluigent’s M-X and 2-X valves. Together, these devices produce high performance fluid automation required for milli and microfluidic applications such as sample preparation, cell sorting, and general liquid handling.
Related Resources & Expertises
5 reasons to choose OEM pressure controllers over OEM syringe pumps for microfluidic applications
Read moreDFC, “Self-Learning” Microfluidic Flow Control Algorithm
Read more- Expert Reviews: Basics of Microfluidics
Key considerations for fluidic system integration
Read more - Expert Reviews: Basics of Microfluidics
Key reliability indicators for OEM components to ensure long-term performance of your flow control system
Read more