Contamination-free Liquid Handling System
- Contamination-free
- No calibration required
- High performance
Introduction to flow sensing
Why pressure-based flow control?
A highly stable and responsible flow rate is often a prerequisite for microfluidic applications. OEM pressure-driven flow controllers were developed to eliminate syringe pump limitations. They in fact can deliver truly pulsation-free flow, enabling greater control accuracy and homogeneity within experiments. In addition, pressure-driven flow control response times are several magnitudes faster than syringe pumps, streamlining the microfluidic process and making possible new flow control regimes.
Sterility requirements and Flow Sensor as a game changer for microfluidic flow sensing
With the growth of biological applications that utilize micro and millifluidics such as cell cytometry or purification for sample preparation, drug screening, organoids, or organs on chips, the need for contamination-free liquid handling systems is expanding. Prior to now, there was no solution for measuring the flow rate in a non-invasive manner.
High fluidic performance using Fluigent contamination-free flow control solution
Today’s Fluigent standard OEM contamination-free liquid handling system, which consists of a high-precision pressure controller and a Non-Invasive Flow Sensor, brings excellent flow rate regulation without needing fluid calibration. The NIFS allows contactless live flow rate monitoring and regulation.
Contamination-free liquid handling system based on pressure-driven flow for microfluidic applications
Components and setup
- Non-Invasive Flow Sensor : The OEM non-invasive flow sensor (NIFS) is dedicated to flow rate monitoring and control. When combined with Fluigent pressure controllers[1] [2] , it allows pressure-based flow rate control without fluid contact, and no liquid calibration needed.
- Modular OEM Microfluidics Flow Controller – F-OEM: High performance, efficiency, and wide pressure and flow rate ranges support the most demanding industrial applications, including microfluidic and nanofluidic applications (microchannels, nanochannels, capillaries, lab on a chip). The F-OEM is a standalone, modular platform that will perform complex fluidic operations.
The components used in this technical note are shown below. The F-OEM pressure controller (1) consists of an electronic board coupled with a pressure module. A pressure supply is connected to the F-OEM pressure module. The NIFS is pneumatically connected between the pressure manifold and its dedicated reservoir. Pressure pushes the liquid through the liquid tubing, which subsequently flows into the microfluidic chip dedicated for cell culture under perfusion.
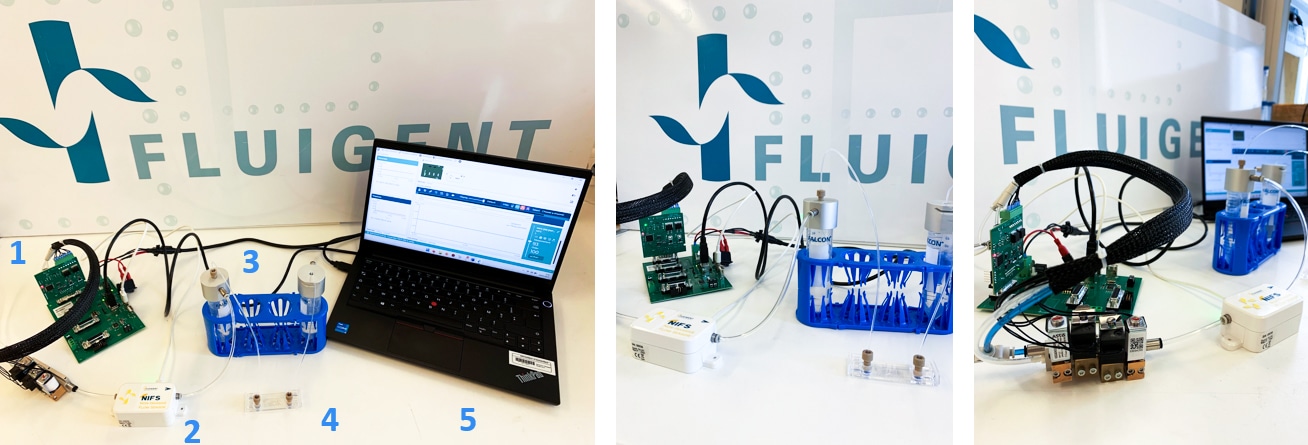
Item | Description |
1 | NIFS – Non Invasive Flow Sensor |
2 | F-OEM Pressure controller |
3 | P-CAP Reservoir |
4 | Microfluidic chip dedicated to cell culture under perfusion |
Fluigent’s dedicated algorithm and software for live liquid flow rate monitoring and control
With the use of an internally developed algorithm, liquid flow rate can be monitored and regulated through Fluigent OxyGEN software and SDK for full system integration. To demonstrate the capabilities of our contamination-free liquid handling system based on pressure, flow rate steps and flow rate stability are explored for a range of different flow rates.
Performance of Fluigent contamination-free flow control system
Flow rate range: a machine learning -based algorithm
The first test shows flow rate steps ordered using a time period of 45 s. Ordered flow rates are 100, 200, 300, 400, 500, 600, 500, 400, 300, 200, and 100 µL/min.
The figure 1 shows the regulated flow rate using the NIFS coupled with the F-OEM. The first flow rate command (100 µL/min) takes about 30 s to reach the targeted flow rate, with an intermediate learning pressure and flow, where the algorithm «learns» from the measured flow rate or pressure couple the hydrodynamic resistance of the system. Through this learning, the following steps are accurately reached, possibly with minor iterations to adjust the targeted value. This behavior can be observed with the next targeted values. From the flow rate graph, we observe it takes < 10 s to reach the next flow rate. Note the liquid flow rate has physically reached the targeted value < 1 s after the pressure change (which can be shown by adding a flow sensor on the fluidic line).
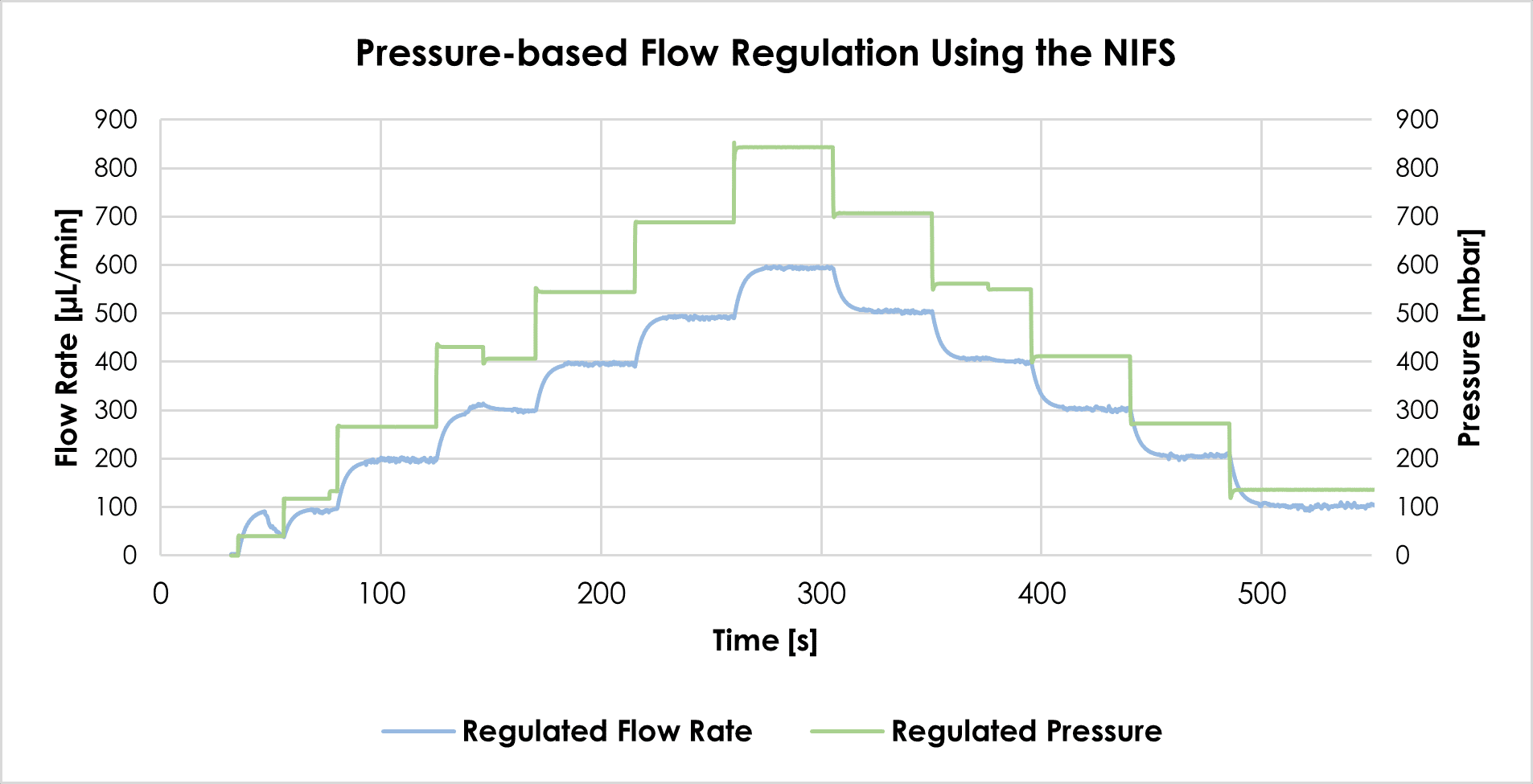
This behavior can be explained by a necessary smoothing step implemented into our algorithm that is based on average values of the gas flow rate that slightly virtually increases flow rate reading.
Flow rate stability
Stability at 200 µL/min
Flow rate stability is studied for 10 min. The figure below shows both the regulated liquid flow rate and pressure using our contamination-free liquid handling system. Flow rate average and standard deviation are respectively 197.9 +/- 3.0 µL/min, securing a < 5% accuracy as mentioned on the NIFS datasheet. The results obtained make the NIFS viable for a large scope of microfluidic applications in this range of flow rates, notably cell cytometry, or for certain types of cells for perfusion.
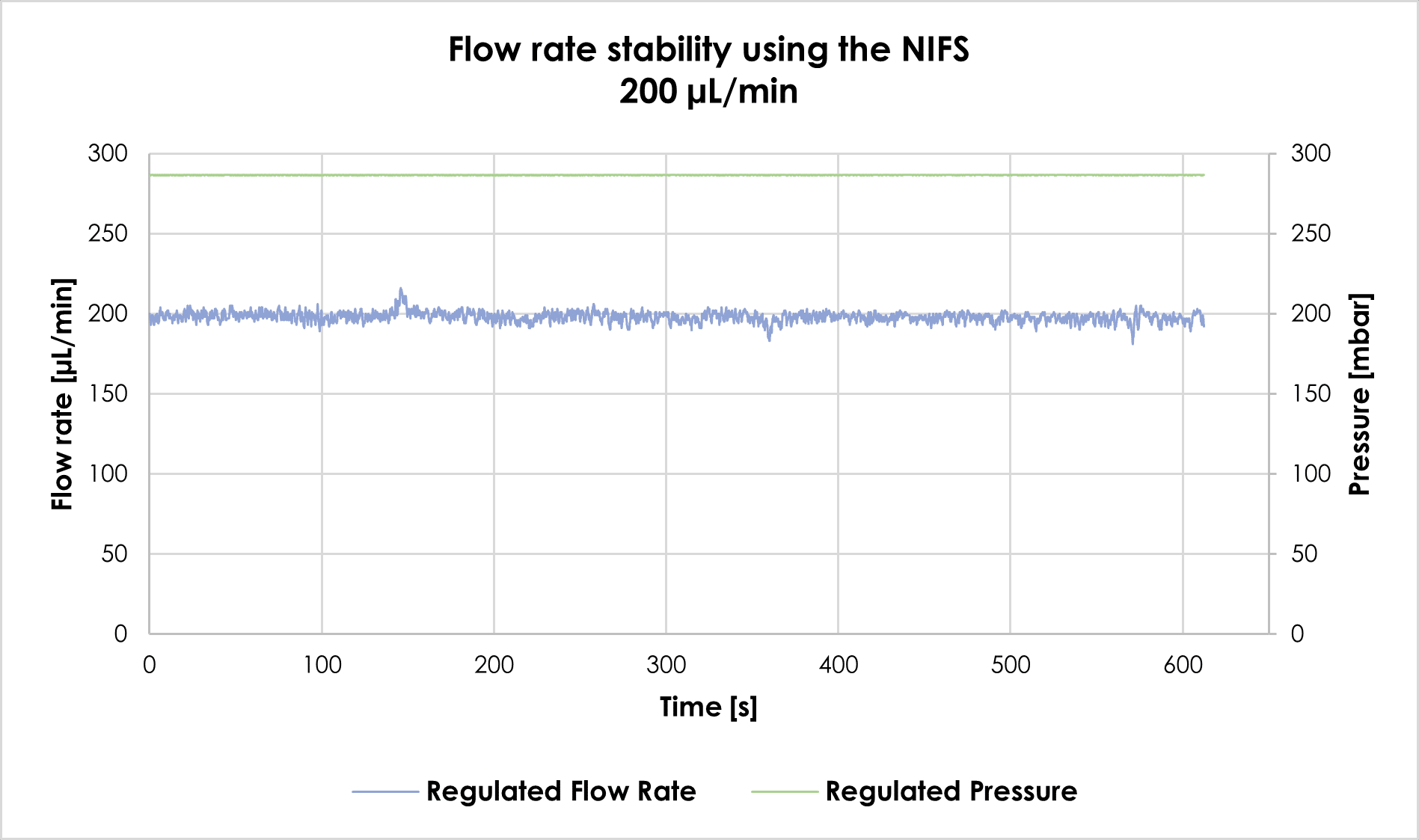
Flow rate stability at 50 µL/min
The 5% accuracy specifications provided on the NIFS datasheet are ensured for flow rates ranging from 100 µL/min to 10 mL/min. It is however still possible to perform flow rate monitoring and control below 100 µL/min with our contamination-free liquid handling system with potentially degraded performance. This is illustrated in figure 3, where 50 µL/min flow stability is measured for more than 250 s. Flow rate average and standard deviation are respectively 52.4 +/- 2.8 µL/min. This makes the measurement slightly above the 5% accuracy provided on the 100 µL/min – 10 mL/min range, but can still be acceptable flow accuracy and precision for several microfluidic applications, especially for cell perfusion or other biological applications where sterility is a prerequisite. The NIFS coupled with a F-OEM is a contamination free liquid handling system, and is a great alternative to invasive systems where highly accurate flow is not mandatory. In addition, the technology is based on gas flow rate measurements, leading to minor gas flow rate instabilities, but do not have an impact and are not observed on the fluidic line.
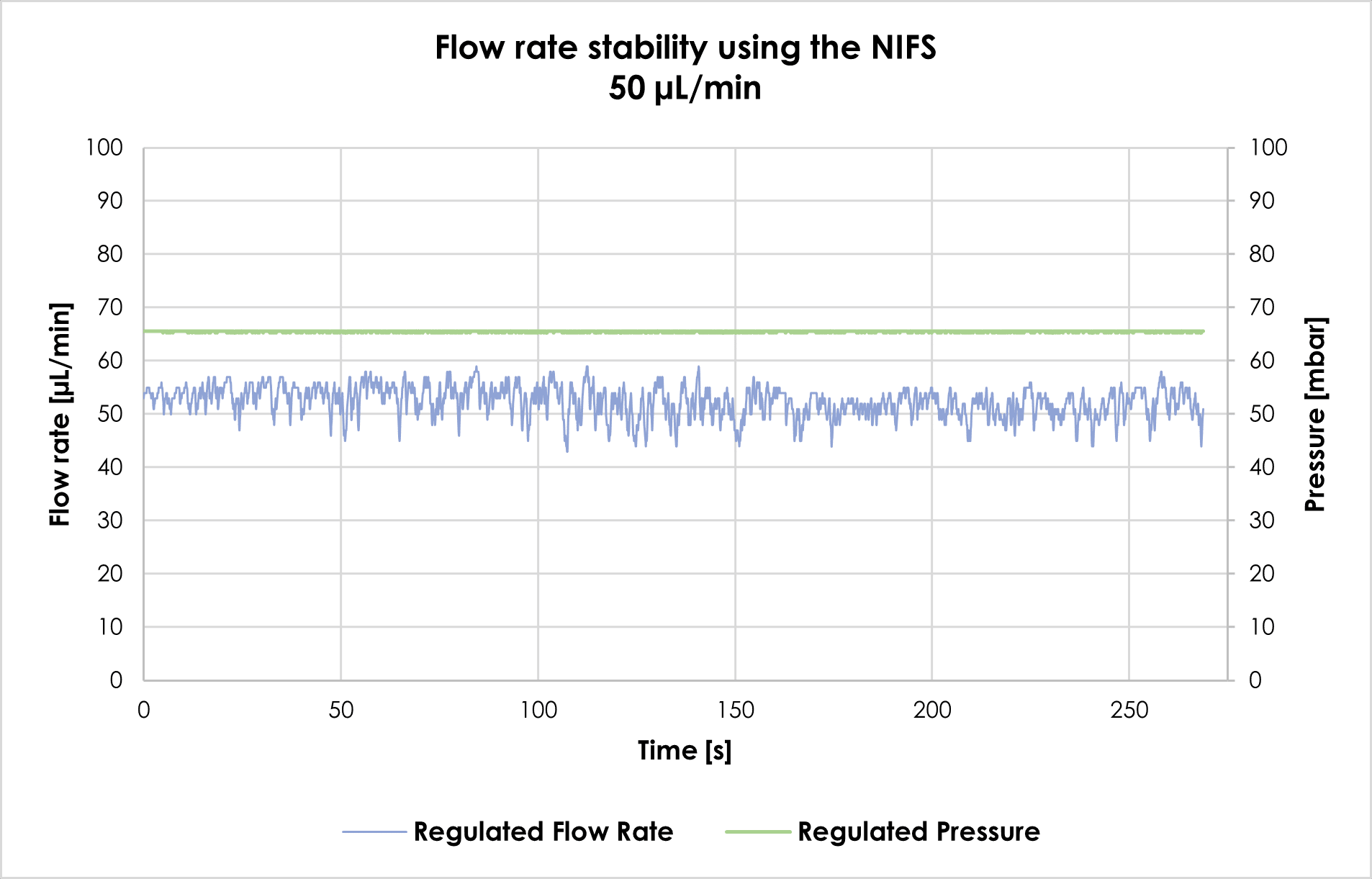
Conclusion
The use of our contamination-free liquid handling system consisting of the NIFS coupled with the F-OEM pressure controller is demonstrated in this technical note, achieving flow rate steps in a range of 100 – 600 µL/min and flow stability of 200 µL/min and 50 µL/min. Fluigent’s standard OEM pressure-based flow control solution, which consists of a high-precision pressure controller and a Non-Invasive Flow Sensor, brings great flow rate regulation without fluid calibration. The NIFS allows contactless live flow rate monitoring and regulation. This unique system combination offers the advantages of pressure-based flow control without the inherent limitations of inline microfluidic flow sensors.