Instrument Stability in Microfluidics
Microfluidics is well-known for the control it offers over flow parameters. By using microfluidic instruments, one can precisely regulate flow rates, pressures, and shear-stress with unmatched accuracy. However, the different types of flow generators all have different stability potential. To ensure good reliability and repeatability for your experiments, it is important to select a microfluidic instrument with high stability.
Definition and comparison of flow control stability metrics
Instrument stability in microfluidics refers to an instrument’s ability to maintain a certain physical property at a constant value, while eliminating any perturbations in the environment. This is a very important parameter, as even small variations in physical quantities during microfluidic experiments can dramatically change the results. A stable instrument, like our pressure-based flow controllers, ensures that results are repeatable and reproducible.
Measuring the stability of microfluidic flow control instruments
The stability of a microfluidic instrument can be quantified by setting the microfluidic instrument to a constant value, measuring the physical quantity across a period of time and using statistical measures of dispersion on the samples acquired. We generally use the three metrics below.
Range
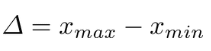
Standard deviation
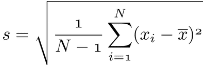
Coefficient of variation
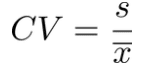
Xmax: Highest measured value | N: Number of samples | s: Standard deviation |
Xmin: Lowest measured value; | X: mean of samples | X: mean of samples |
Unit: same as the sample | Unit: same as the sample | Unit: dimensionless |
1. Using the range metric to measure stability of microfluidic flow control instruments
This metric is the difference between the highest and the lowest value measured during the characterization. It is sensitive to outliers and not very representative of the microfluidic instrument’s stability, but it can be important if the experiment has narrow specifications and can be disturbed or damaged by deviations, even for a short amount of time.
2. Using the standard deviation metric to measure flow rate stability
The standard deviation metric represents an estimate of the typical distance between each sample and the mean. It is more representative of the microfluidic instrument’s stability than the range, as it gauges performance across all data points.
3. Using the coefficient of variation to measure stability in microfluidics
The coefficient of variation metric is the ratio of the standard deviation to the mean of the samples. It is the most useful value to characterize a microfluidic instrument’s stability, as it is independent of scale and unit.
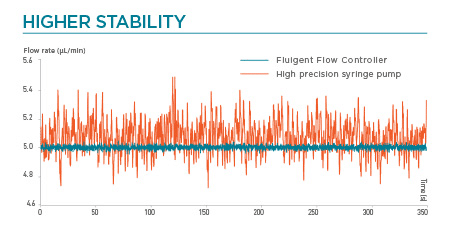
What are the resolution and response times, and what is their effect on the microfluidic flow control instrument’s stability?
In microfluidics, a flow control instrument’s stability depends on the resolution and response time of its sensors and actuators, as well as the algorithms for communication and feedback.
Resolution
The resolution is the smallest difference in the physical quantity that the sensor is able to detect, or the smallest variation that can be produced on the actuator’s output. The better the resolution, the more closely the microfluidic instrument can follow its inputs and control its outputs to regulate the quantity of interest.
Response time
The response time refers to the time it takes for the sensor to produce a new reading, or the time it takes for the actuator’s output to reach the requested value. The shorter the response time, the faster the instrument can run its feedback loop to compensate for any variations in the quantity of interest.
Pressure regulators improve instrument stability in microfluidics
The stability provided by pressure regulators for microfluidics is generally better than the resolution of the internal pressure sensor,due to a technique called oversampling. By reading the sensor at a very fast rate (from 1000 to 2500 Hz), the microfluidic instrument obtains multiple samples corresponding to the same real pressure value, since the pressure changes at a slower pace. These samples contain electronic noise inherent to the sensor, but that noise is zero-centered, which means we can greatly attenuate it by averaging the samples, thus achieving a more precise measurement of the pressure. The regulation algorithm uses an integrator, so it naturally averages the sensor measurements and is able to maintain the pressure with a dispersion much smaller than the sensor’s resolution.
However, the main quantity that must be regulated in microfluidics is the flow rate, as it is a parameter that regulates molecule transport, shear-stress, or droplet formation. A stable pressure is often not enough to maintain a stable flow rate. For microfluidic chips with a low fluidic resistance, the pressure required to maintain the flow is small, so any changes in the height of liquid inside the reservoir (either because it emptied over time or because it was moved during the experiment) will change the flow rate due to the hydrostatic pressure. The pressure used for most experiments is 10 mbar (0.15 PSI).
On the other hand, if the channels in the microfluidic chip are very narrow, they can become clogged with particles, thus increasing the fluidic resistance and decreasing the flow rate if the pressure remains constant. These particles can come and go at random, leading to an unpredictable flow rate.
This is why Fluigent also offers microfluidic flow rate sensors and regulation algorithms. When used with pressure regulators, microfluidic flow rate sensors can maintain the desired flow rate and eliminate any pneumatic or fluidic perturbation. Microfluidic flow rate sensors achieve the same functionality as a syringe pump, but with a much more stable and reliable output.
To obtain the best stability for your microfluidic experiments, be sure to select instruments with the appropriate range (visit our microfluidic calculator for more information). It is possible to add fluidic resistance to your microfluidic setup to increase the amount of pressure necessary to produce the desired flow rate and more closely match the range of the experimental setup to that of the instrument.
Related content
Flow EZ™
Read moreMFCS™ series
Read morePush Pull
Read moreFLOW UNIT | FLOW UNIT +
Read moreConcepts of microfluidics
Read more- Support & Tools
Pressure & Flow Rate Calculator
Read more - Support & Tools
Shear Stress Calculator
Read more - Expert Reviews: Basics of Microfluidics
Application of microfluidic chip technology
Read more - Microfluidics White Papers
An exploration of Microfluidic technology and fluid handling
Read more